Cover Story
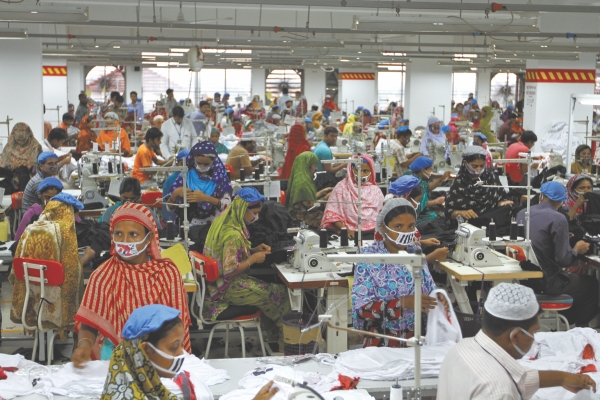
A Stitch in Time
Bangladesh's RMG sector is the country's one of the highest foreign exchange earners. It has also been at the heart of controversy recently because of worker unrest in some of its factories. The huge amount of toxic waste that these factories have been dumping into the water bodies has also been a bone of contention for environmentalists. In the midst of all this is an inspiring example of how environment friendliness and profitability can be made perfectly compatible.
Naimul Karim
Photos: Amirul Rajiv
While the garments industry holds the centre-stage of the country's economy, it also consumes a lion's share of our energy resources and is responsible for releasing huge amounts of toxic wastes into the rivers and other water bodies.
According to a World Bank study, the four major rivers near Dhaka– Shitalakhya, Balu, Turag and the Buriganga– receive more than 1.5 million cubic metres of wastewater every day, from the surrounding industrial units. The report suggests that the improper treatment of the wastewaters by a number of factories, result in the discharge of highly toxic wastes that cause serious damage to the ecology and aquatic life.
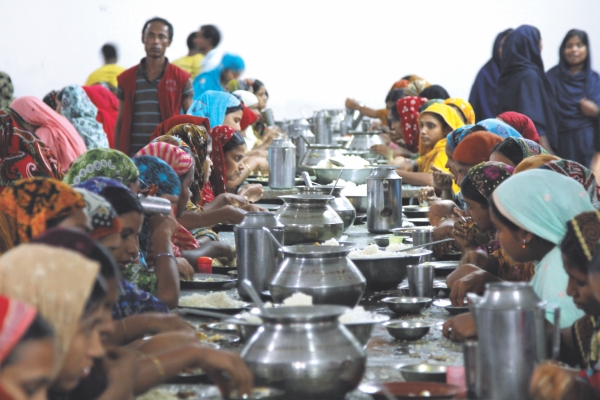
Garment workers at Echotex Ltd are served lunch everyday at the factory.
The main source of pollution, environmentalists claim, comes from the dyeing section. Majority of the dyes, used to add colours to the fabrics, are non-biodegradable and hence, the resulting 'dye waste' ends up in the environment. The chemicals used to produce dyes are often highly toxic, carcinogenic, and can even be explosive.
Fortunately though, contrary to popular belief, there are a number of garment factories that strive to create a balance between their rate of production, the workers' issues and the environmental crises.
"When we initially set up our factory in Gazipur, we decided that we'd only start the dyeing process after our effluent treatment plant (ETP) was ready. Currently, our ETP is in the first stage. The waste from our industry goes through a series of chemical and biological reactions before getting discharged,” says Mohammed Bin Quasem, Director of Echotex Ltd, a garments factory, which recently received a national award for its ETP.

Supporting Quasem's statement are a number of fish aquariums, right next to the ETP, set-up with the treated effluent. "As of now, the effluent doesn't affect the aquatic life. We plan to upgrade our plant in the coming years. Once we reach the second stage, i.e. Reverse Osmosis, people can actually drink the water from the discharge," he adds.
The new target, however, requires a lot of investment. "We need to spend around 4 to 5 crores. Almost as much as some people invest for the entire factory," he claims. According to Quasem, the huge investment in the factory's waste management system has given them many rewards.
"Nowadays, many buyers actually care about the environment and the workers. They have a look at the entire factory, analyse the way it runs before signing a deal with us. We maybe a tad more expensive compared to others, but at the end of the day we have won many contracts because of our disposal system and the way we treat our workers," claims Quasem.
As it so happens, chemically filtering the waste isn't enough. Following the processes at the ETP, a secondary waste-product, known as sludge or a cake, is formed. The particular waste product is extremely difficult to dispose. The sludge is taken out of the ETP, solidified, compressed and stored in separate tanks.
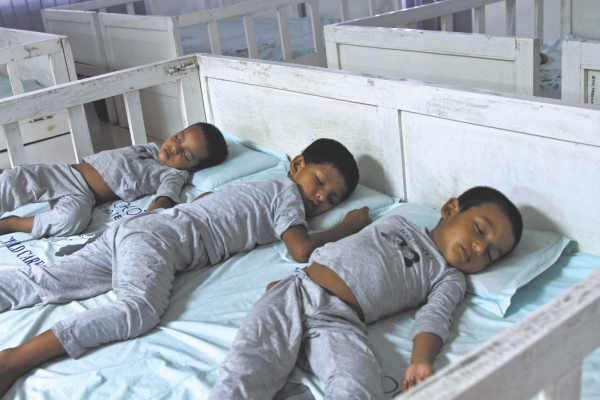
|
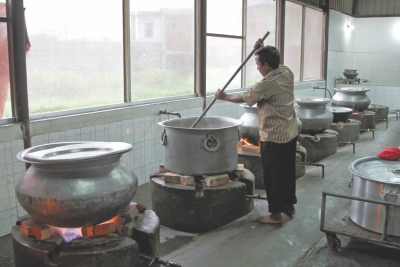 |
|
The factory kitchen cooks 11,000 KGs of rice everyday and has employed 90 people in the kitchen alone. |
"We are extremely worried about the cake. It contains a lot of toxic chemicals. If you dump it, it's going to pollute the rivers. If you burn it it's going to cause air pollution. So basically, we've been storing them ever since we started the ETP," explains Quasem. The company states that they gather close to four tons of sludge every month.
In a bid to find a way to dispose the sludge in an environmentally safe manner, Echotex Ltd recently signed a Memorandum of Understanding with the Bangladesh Atomic Energy Commission (BAEC). Through this deal, the garments company hopes to find a way to appropriately dispose of the solid waste. "The BAEC claims that they can convert the sludge into a kind of fertiliser that can be used for farming. It'll be a great breakthrough if our venture is successful" says Quasem.
While there are legal provisions to ensure that heavy garment factories build effluent treatment plants, there are however, no outlines or rules provided to take care of the sludge created due to the ETPs. As a result, industries dispose them in their own way.
"Majority of the industries just dump them in the rivers. Perhaps what's more dangerous is that some of industries send the cakes to brick kilns where they burn it along with coal. These waste products contain various chemicals which if burnt can actually lead to acid rain," claims Dr Mubarak Ahmed Khan, Chief Scientific Officer, Institute of Radiation and Polymer Technology. "Countries like Mexico have already witnessed these rains and we are headed that way," he adds.
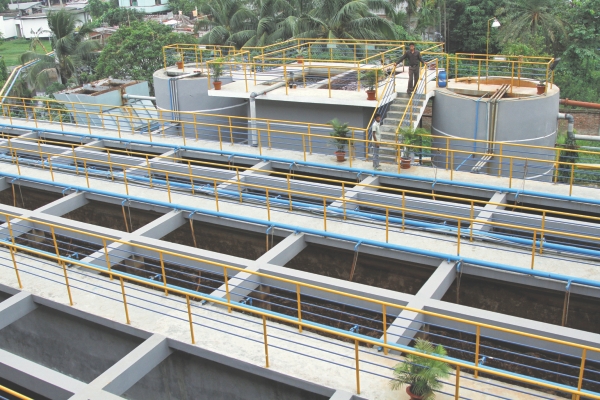
The effluent treatment plant at
Echotex ltd was given a national award.
With an aim to find an environment-friendly method to dispose of the sludge, the Department of Environment (DOE) recently signed an agreement with a German development organisation. "We'll be getting a guideline from them for the next two to three months. We have also sought the help of the Bangladesh Atomic Energy Commission, who plan to treat the waste-water through radiations," explains Dr Sultan Ahmed, a senior member of the DOE.
|
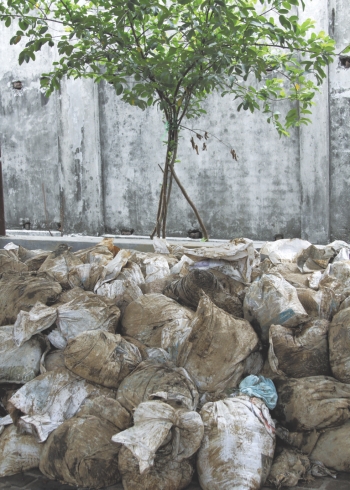 |
|
The disposed sludge kept in tanks. |
The DOE recently fined a number of factories for disposing toxic waste into the rivers. Dr Ahmed, however, admits that the enforcement team of the DOE finds it difficult to monitor the waste-disposal system of the factories. "Since a factory is required to build an effluent treatment plant in order to be permitted to set up a heavy factory, we can give you the records of the number of factories that contain ETPs. However, we don't know for sure if they are running them every day, since it's a very expensive procedure," Dr Ahmed adds. Echoing Dr Ahmed's views, Dr Khan says, "It costs around TK 60,000 to 70,000 per day to run the ETPs; so, many industries don't bother to purify the effluent every day."
Bearing in mind the problems faced by factory owners with regard to sludge management, the MoU signed between Echotex Ltd and the BAEC--which is the first time a private company has decided to work in tandem with a government organisation in this field– can lead to a great breakthrough in the garment industry.
Apart from working on different waste management schemes, Echotex Ltd has also taken up various energy saving projects. One of the steps includes the use of LED lights for sewing machines. “While surveying the factory, we realised that attaching these lights on the machine would work better than putting up an extra overhead light bulb,” says Quasem. The factory has also uses different forms of steam energy while dyeing which saves fuel.
A glance through the facilities provided by the Gazipur-based company spells huge investment. A gigantic dining space to accommodate around 6000 workers, massive working spaces, the presence of a proper fire-exit system, the company's very own medical clinic, a day care centre for the employees' children, the provision of boiled eggs—for extra protein– during the evenings hearty lunches -- all this gives the impression of high ethical and technical standards. “ We obviously have an aim behind these investments. We want our workers to be in good health so that they can work better,” says Quasem.
The recent protests in Ashuliya, which led to the closure of more than 300 factories, has reinforced the importance of a proper communication system between the employees and the stakeholders. A positive aspect of the company is the presence of a proper 'Workers Participatory Committee', a mini version of a labour union. “There are 50 representatives in the committee and they meet once a month. After discussing the different grievances and their demands, they meet the management team. We meet them once in two months. After which, we negotiate and come to a decision,” explains Redwan R Chowdhury, Director, Echotex Sourcing.
Stating an example, he says, “Earlier we used to provide beef twice a month. During a committee meeting we got to know from the workers that they preferred more meat in their lunch. From then on we have been serving meat once a week.”
The meetings eventually lead to the creation of various incentive packages to encourage work productivity amongst the labourers, “The committee told us that they prefer working overtime in order to earn some extra money. So then we told them that if they increased their productivity within the regular hours, we would pay them extra. For instance, the workers today finish twelve hours' worth of work in ten and they get paid for the extra hours. It's a win-win situation.” says Quasem. The company also took a firm stance against verbal abuse, a dominant problem in these industries. “Supervisors in this field are usually rude while talking to the labourers. So we stated that if we receive any complaints against them, then they wouldn't get the extra money.”
The above examples prove the importance of maintaining a close relationship with workers. “It's always important to know what goes on in the minds of the workers," especially when you have factories closing down and workers protesting in other areas," says Aysu Mehbuba Rahman, Assistant General manager of Far East Knitting and Dyeing Industries Ltd, another garments company that has been acclaimed by many international buyers. "Fortunately, we have managed to close the gap, as a result, we haven't faced any major problems ever since the factory's inception."
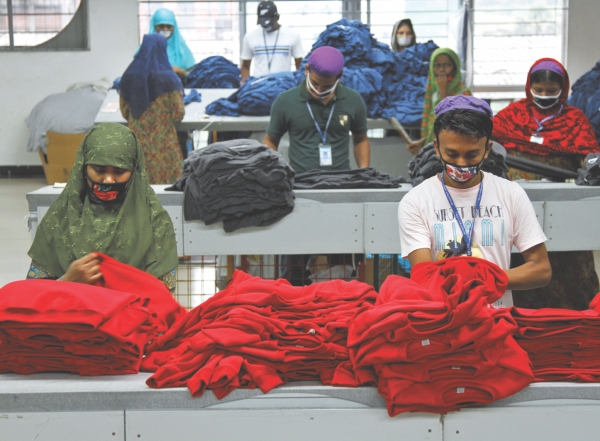
A workers’ participatory committee bridges the gap between the workers and the owners.
Amidst vulnerable times in the RMG arena of Bangladesh, companies like Echotex Ltd have managed to stand apart, both in terms of addressing the labourers' issues and working on an environment –friendly scale. They have proved that it is, indeed, possible to run a factory on ethical grounds and operate without violating the workers' rights. With the constant protests in the garments industry posing a threat to the only thriving sector of the country, one hopes that many more owners emulate similar principles, to protect and sustain what was once known as the golden sector of the country.
A New Solution to Pollution
|
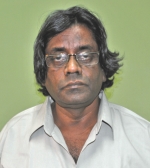 |
|
Dr Mubarak Ahmed Khan, Photo: Courtesy |
Garment industries that have set up proper effluent treatment plants are currently struggling to deal with the secondary waste material, called the sludge or the cake. Dr Mubarak Ahmed Khan, the Chief Scientist Officer, Institute of Radiation and Polymer Technology, however, believes that the usage of radiations to treat the effluents can lead to much better results.
“If an industry regularly runs its ETP, they'll get huge piles of sludge. What's the point of spending so much money on a process that doesn't eradicate all the waste?” questions Dr Khan.
Explaining his research with regard to waste management, Dr Khan says, “We treated the waste waters with gamma radiation and found good results. Radiation induced wastewater treatment can be potentially beneficial in treating industrial and municipal waste water in Dhaka city. This decontaminated waste contains nitrogen compounds and could be used for irrigation. The trees and fruits grown, in our lab, from it turned out fine.”
Dr Khan who is currently working with Echotex Ltd on sludge management believes that the sludge can be converted into a sort of fertiliser in due time. “The sludge contains Nitrogen compounds that can be used as fertilisers, once they are broken down. We are currently trying to find out the exact amount of radiation required to break the molecules,” he explains.
While finding a possible way to dispose the sludge may take time, Dr Khan remains confident that treating the effluent with radiation, before it goes through the ETP, can successfully treat the waste and leave no byproducts. “I believe this can be used in the near future. The problem, however, is that the local companies don't trust my idea, since it's comparatively new. So I ask them to visit countries outside; they are doing work based on the same principle,” he explains.