Green factories brighten image of apparel sector
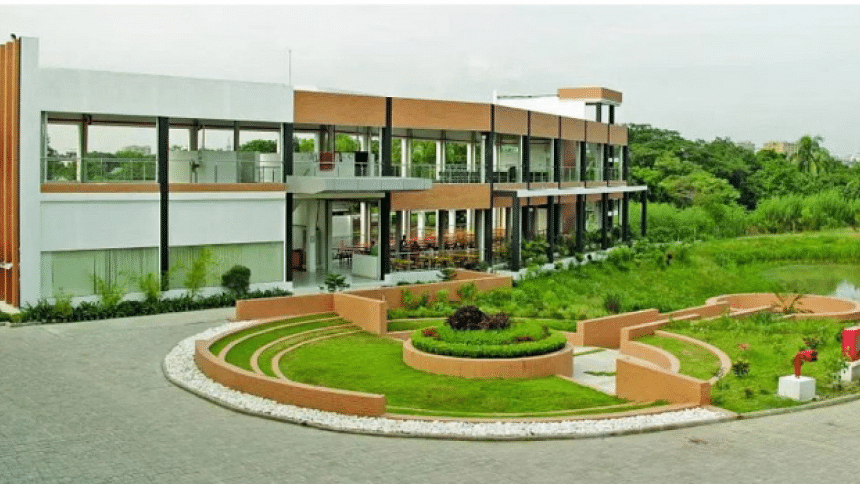
Bangladesh's apparel industry has witnessed numerous ups and downs ever since the deadly fire at the Tazreen Fashions factory in Ashulia and collapse of Rana Plaza in Savar about a decade ago.
Following these two disasters, the industry underwent massive reforms while also being made to withstand the severe implications of Covid-19 and now the ongoing Russia-Ukraine war.
Still, it has defied the prolonged global economic downturn as export earnings from the sector remain in the positive territory.
The apparel industry's strong showing over the years mainly comes down to two reasons.
First, Bangladesh has implemented remediation measures to strengthen workplace safety as suggested by the Accord on Building and Fire Safety in Bangladesh and Alliance for Bangladesh Worker Safety.
Second, Bangladesh continued suppling apparel products even during the Covid-19 pandemic, when most factories across the globe had shut down.
These two factors boosted the confidence of international retailers and brands in regard to the domestic apparel industry. As such, the country has performed well at a time when most garment producing nations are struggling to keep the business afloat.
As a part of their sustainability and workplace safety initiatives, local suppliers had started building green garment factories in hopes of brightening the sector's image.
This is because Western buyers were avoiding Bangladesh as a sourcing destination after the two industrial disasters in 2012 and 2013 exposed the poor state of labour rights and environmental compliance in the sector.
At the time, consumers in the EU and the US were seen protesting outside various retail outlets, urging them not to buy the "blood-stained garment items made at sweatshops in Bangladesh".
But within the span of about 10 to 11 years, Bangladesh has become home to half of the top 100 green industrial units worldwide.
Being the global champion in green factories certified by the Leadership in Energy and Environmental Design (LEED) programme of the US Green Building Council (USGBC), there are 63 platinum rated garment units in the country.
Meanwhile, another 110 are gold rated, 10 are silver rated and four are just certified.
Platinum certification is the highest category in the ranking system while gold is second and silver is third. The fourth category is for industrial units that just meet the minimum requirements.
Besides, more than 500 other garment factories are awaiting LEED certification for their green initiatives, according to the Bangladesh Garment Manufacturers and Exporters Association.
China has the second highest number of platinum rated factories with only 10 while Pakistan places third with nine.
Other global leaders in LEED certification include India and Sri Lanka with six each while Taiwan and Vietnam have four.
Myanmar and the US each have two platinum rated factories while Ireland, Italy, Indonesia, Mexico, Poland, Paraguay, Romania, Turkey and the UAE have one apiece, as per data from the USGBC.
The data shows that Bangladesh is far ahead of major players such as China, the world's largest apparel supplier, when it comes to implementing green initiatives as the country boasts one of the lowest industrial carbon emissions.
However, international buyers do not pay additional or premium prices for apparel sourced from green factories as they believe it is mandatory to take up such initiatives.
This begs the question as to why local suppliers should continue investing heavily on green units when they do not receive any immediate benefit.
Compared to traditional factories, it costs 20 per cent more to set up a green unit.
But rather than worry about getting additional prices, most green factory owners say they set up their units following relevant guidelines in order to brighten the sector's image and foster long-term relationships with buyers.
The green initiatives taken by local garment makers has helped convince Western consumers that workplace safely has improved greatly as LEED certification is only given through a rigorous process that ensures strict adherence with the guidelines.
Maintaining the required compliances, especially in regard to environmental sustainability, also helps the factories save more than 30 per cent on energy costs and water consumption.
As such, LEED certification has become a tool for marketing locally made garment products as suppliers say foreign retailers and brands give priority to green garment factories when placing work orders.
So, it can be said that garment suppliers could care less about securing additional prices for their green initiatives considering the other advantages on offer.
Comments