Turning plastic wastes to resources
A grim future threatens the whole world, especially the lives of thousands of species, including humans, as we keep polluting the environment in many ways. Pollution from plastic wastes is one of the biggest threats at present. However, there is still hope to save the day by turning these plastic wastes into resources.
For a country like Bangladesh, which is already threatened by the adverse effects of climate change, the accumulation of plastic wastes in our land and water and the pollution caused by this pose a grim reality.
Yet, there is still light at the end of the tunnel.
We have so far tried various ways to dispose of plastic wastes -- recycling, incinerating, dumping at landfill sites, and reusing those in some alternative ways. However, none of these proved to be efficient in the context of Bangladesh yet for different reasons.
According to the Department of Environment, the country produces around 381 tonnes of plastic waste every day, out of which around 143 tonnes can be recycled. This basically means that only 38 percent of the plastic is recyclable.
One reason why recycling proved to be inefficient is that the wastes are not dumped in an organised way. Different types of plastic products are often dumped together at the same place, thus accumulating there in tonnes and making it difficult to sort between the different types to ease the recycling process. This often raises the cost of operation too, thereby making very few interested in this business.
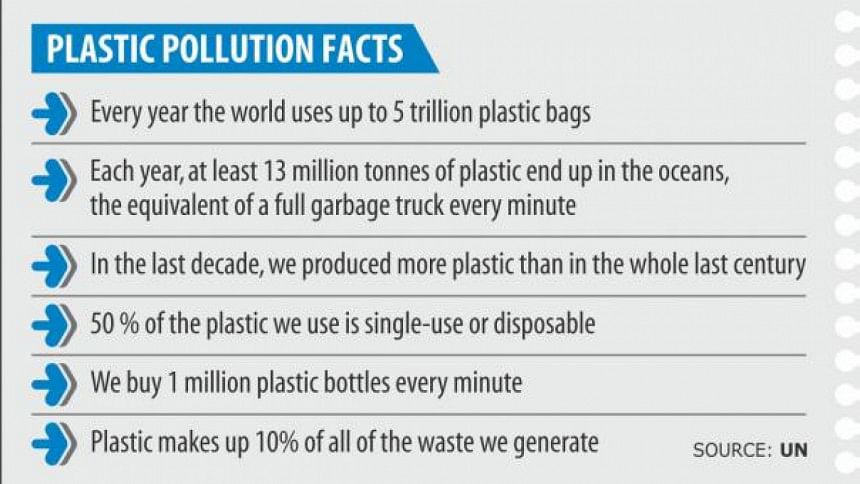
Dumping the wastes at landfill sites is not a good option either, as the wastes would not decompose, at least in a thousand years or so, and instead stay there making the land unusable for any productive purpose while the wastes sometimes pass on to the nearby water channels during rains and flooding.
Meanwhile, incineration is a faster and easier way to dispose of the wastes, but probably equally damaging to the environment in the same way as dumping them around, as the fumes from the burning plastic include many toxic gases, including some of the most potent greenhouse gases, which pollute the air to a significant extent.
However, we can contain the fumes and turn those into black soot which can be processed to produce ink. The ash from incineration of the wastes can be used to make bricks, just like what Ethiopia is doing.
So far, existing ways of containing plastic wastes have not been greatly rewarding to those who are involved in it, and hence the operations failed to move on to larger scale. This is why not many are interested in getting involved in a business dealing with wastes.
It is time we learn from what other countries are doing to fight against this worst ever man-made disaster to environment.
If we look at Sweden and Germany, the two countries which are recycling wastes, especially plastic wastes most efficiently, we would find that they are using their wastes for incineration, but in a process which will generate energy. The process, namely waste-to-energy, is quite a profitable one and is capable of producing energy in the form of electricity in quite the same way as a thermal power plant works, only using plastics instead of fossil fuel in this case.
Since we have a huge demand for electricity in the country, we may consider burning the wastes to produce power to run the industries and factories, thus allowing them cheaper electricity and enabling them to flourish.
We could then look at what our neighbour, India, is doing. In India, roads are now being made in different states with bitumen made from plastic wastes, and the roads have so far worked out pretty well and durable. We are in dire needs of good roads and turning the plastic wastes to bitumen for road construction might be an effective mean to kill two birds with the same pebble.
But the most profitable way to turn plastic wastes to resources is probably by turning those to oil by thermal cracking, a chemical process.
Plastics are mainly petroleum-based polymers, which means in basic form they are just some petroleum products. Any type of plastic wastes can be turned back to petroleum under conditions of certain temperature and pressure. The petroleum produced is in an amalgamated liquid form, which can then be separated into different products with specific uses.
A start-up in UK, Recycling Technologies, is using this very idea to get rid of the country’s plastic wastes. They are collecting the wastes, shredding them, then passing them to a machine they have developed for the process to produce a petroleum-based liquid they have named Plaxx, which is a low sulphur based synthetic hydrocarbon with a high calorific value. This Plaxx is then separated into four different products: naphtha substitute/light oil (Plaxx-8), low sulphur heavy fuel oil (Plaxx-16), base oil (Plaxx-30), and wax (Plaxx-50).
The naphtha substitute/light oil (Plaxx-8) can be used by plastics manufacturers and petrochemical companies as a raw material for virgin plastic production as they look to increase the recycled content of their end products.
The low sulphur heavy fuel oil (Plaxx-16) can be used as a clean fuel compliant with the MARPOL Regulation for marine operators and Medium Combustion Plant directives. It has low sulphur, higher viscosity and is a competitive substitute to fuel for marine engines, and also for large-scale heat and energy generation.
Plaxx-16 is a heavy fuel oil with low sulphur content, while Plaxx-50 is being developed as a commodity paraffinic wax, which can be used as raw materials to manufacture coatings and environmental protection, injection moulding and mould release, bitumen modifiers, and candles.
The start-up’s flagship machine, RT7000, utilises an advanced thermal cracking technology to offer environmentally responsible solution at the lowest cost for end-of-life plastic.
The machine has been designed as a transportable, modular, mass-producible unit, with a limited footprint of 900 sq. metres, which allows it to be easily located on existing sites where the wastes are dumped, largely avoiding the cost of transportation.
Its modular nature makes it suitable for sites with smaller or larger waste handling capacities. Each unit is capable of processing a standard 7,000 tonnes per annum. Larger output can be accommodated by multiple units installed in parallel.
The start-up also offers to build and operate the RT7000 units at the site for those who would look to this recycling solution to plastic waste handling.
This indeed looks like a beacon of light at the end of a tunnel. All we need is someone to buckle up and move ahead in the direction of that ray of hope.
Comments