Building Vulnerability Assessment Process in Bangladesh
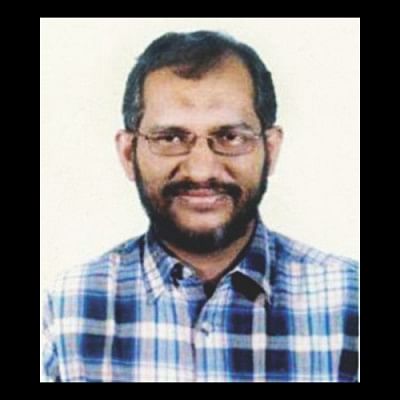
In Bangladesh ready-made garment (RMG) industry is one of the most important export-oriented business sectors, which is facing challenges to ensure workplace safety. Rana Plaza collapse in Bangladesh is the consequence of such non-compliance. The accident resulted in different local and global initiatives to address the challenges. One such initiative is the EU initiated Sustainability Compact. One of the main actions recommended by this initiative is assess to the structural and fire safety of all active export-oriented RMG and knitwear factories and initiate remedial actions. This paper describes the structural assessment process followed by National Tripartite Action Plan (NTAP) to fulfill the action recommended by the Sustainability Compact.
Manmade industrial disasters happen frequently in Europe, resulting in adoption of minimum requirements for safety and health protection at the workplace to prevent accidents and occupational diseases. Without workplace safety compliance, it is almost impossible to ensure business sustainability and thus to survive in global market competition (Rajon, 2014). Despite the challenges in RMG sector in Bangladesh McKinsey, a global management consulting firm, described Bangladesh as the next hot spot in apparel sourcing (Berg et al., 2011). The firm forecasted that the export-value growth will be 7-9% annually resulting in increase of apparel export doubled by 2015 and nearly tripled by 2020, if the sector in Bangladesh can ensure total compliance with the international standard. Even after the Rana Plaza collapse, a study jointly conducted by the United States Fashion Industry Association (USFIA) and the University of Rhode Island (URI) revealed that, the US-based fashion companies are expected to boost their sourcing from Bangladesh by 2016 (Lu, 2014).
This work is about the progress of disaster risk reduction in RMG sector through addressing workplace safety issues with special focus on resilience of factory buildings. In this regard, this paper aims to review and discuss in detail about the action regarding structural assessments of buildings housing RMG factories in Bangladesh including its progress, implementation mechanism, and outcomes within two years after Rana Plaza collapse to bring out the progress of disaster risk reduction in this sector. Assessment of buildings is not an end in itself, which requires further study to take corrective measures accordingly. So, along with the discussion, some recommendations have been suggested in this study to be incorporated in the structural assessment initiative to make the weak factory buildings resilient by addressing the structural issues.
RANAPLAZA BUILDING COLLAPSE
Just months after the fatal fire at Tazreen Fashions, Rana Plaza collapsed on 24 April 2013 at around 8:30 am, which was located at Dhaka-Aricha highway near Savar bus stand (Figure 1). It is the last most alarming accident in RMG sector in Bangladesh, which resulted due to the reluctant attitude of the stakeholders towards the compliance issues.
Rana Plaza housed five garment factories employing around 5,000 people, 300+ shops, and a bank. It was a 9-storied industrial building with a single basement. Figure 1 shows the schematic diagram, of the building and a photo before it collapsed. Instead of RAJUK (Capital Development Authority), local municipality (Savar) gave permission to the owner of Rana Plaza to construct a five storey commercial building with one basement in 2005 and later allowed the owner to extend it up to nine storey, without considering the structural design, though the foundation of the building was of 5 storey (Rahman, and Ansary, 2013). Moreover, the building was converted from commercial to industrial use, and power generators were placed at the higher floors. As a result of such violation in building construction, cracks developed on some pillars and a few floors of the building following a jolt on 23 April 2013, a day prior to the fateful day. After inspection of industrial police, they requested the building authorities to close the building and to suspend operations of the factories on that day. However, the building owner and top-management of the garment factories ignored the warning and forced the workers to work in the next morning of 24th April, 2013. As a consequence, the collapse resulted in the high death toll of 1,134 and more than 2500 people to be badly injured at the end of the rescue operation on 14 May 2013. It was a global tragedy emphasizing the importance of issues concerning millions of workers, employers, brands and consumers - the entire supply chain in the RMG sector of Bangladesh.
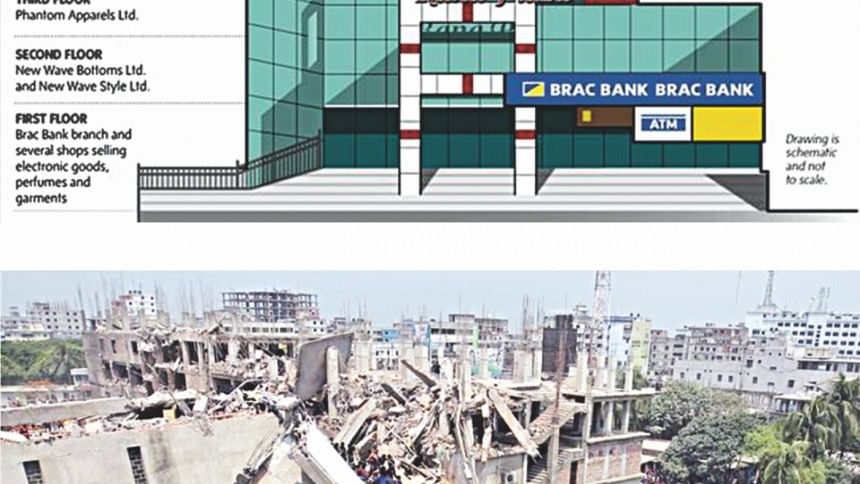
Fig. 1 Rana Plaza collapse on April 24, 2013
STRUCTURAL ASSESSMENTS OF BUILDINGS HOUSING RMG FACTORIES IN BANGLADESH
Progress of the Structural Assessment Initiative
After Rana Plaza accident, work-place safety was considered one of the most important challenges to sustain RMG industry in Bangladesh. Thus actions regarding structural and fire safety assessment of all active export-oriented RMG factories were addressed in all the action plans. The supporting actions included up-gradation and strengthening of the Chief Inspector of Factories and Establishment office to a department, recruitment of additional labour, fire and building inspectors, arrangement of training programs to increase capacity of the inspectors, development of plan in consultation with the ILO to conduct effective inspections, initiation of remedial actions or close or relocate factories as appropriate, and creation of a publicly accessible database of all RMG/knitwear factories as a platform for reporting labour, fire and building inspections.
The GoB has already upgraded Chief Inspector of Factories and Establishment office to Department of the Inspection for Factories and Establishments (DIFE), sanctioning 679 new staff positions including 392 new inspectors and also started organizing training program for the newly recruited inspectors for capacity building. Bangladesh University of Engineering and Technology (BUET) and two private engineering firms TUV SUD Bangladesh (Pvt.) Ltd and Veritas Engineering & Consultant on behalf of the NTC, the Accord, and the Alliance are responsible for conducting the assessments of the structural integrity and fire safety of RMG factory buildings. To undertake the structural assessment of factory buildings with common approach, Guidelines for Assessment of Structural Integrity and Fire and Safety including harmonized standards were developed the technical experts (structural engineers, fire safety experts, etc.) from the BUET on behalf of the NTC, the Accord, and the Alliance. A review panel along with a review mechanism was also established to handle urgent safety issues in garment factories. Finally on November 2013, assessments of the structural integrity and fire safety of RMG factory buildings officially commenced led by engineers from BUET. The BGMEA and BKMEA agreed to share necessary documents related to factory design and layout with the Committee to facilitate a smooth assessment process. A publicly accessible database of all RMG factories has also been created as a platform for reporting labour, fire and building inspections.
Implementation Mechanism of the Structural Assessment To undertake the structural assessment of factory buildings with common approach and standard, ILO brought together the technical experts (structural engineers, fire safety experts, etc.) from the BUET on behalf of the NTC, the Accord, and the Alliance. NTC endorsed 'Guidelines for Assessment of Structural Integrity and Fire and Safety' including harmonized standards developed by technical experts from the BUET, the Accord and the Alliance. The common steps for structural assessment of buildings housing RMG factories by team of expert are described below:
Visual inspections of factory building are done for identification of existence of any distress in the structure of a building.
The design drawings and soil investigation reports of the factory buildings (if available) are reviewed to assess the current use and loading pattern.
Assessment of immediate threat of collapse from current building use is done to take decision about further initiatives required to make the factory buildings resilient. For the assessment of immediate threat of collapse from current building use, the surveyors firstly highlight key columns and carry out simple calculations of working stresses to find out Factor of Safety (FOS), which is Column Ultimate Strength, divided by the Column Working Stress. Here, the Column Working Stresses are calculated comparing data set values and trigger points developed. Column Ultimate Strengths of the key columns of RMG factory buildings are calculated using equation (1) according to Bangladesh National Building Code (BNBC) (1993).
P_n = 0.8?[0.85f?c(A_g-A_st)+f_y A_st] (1)
Where,
Pn = Ultimate Strength of a column
? = strength reduction factor (= 0.7)
f?c = compressive (cylinder) concrete strength
Ag = gross area of concrete section
Ast = area of reinforcement
fy = steel strength
To decide on Column Ultimate Strengths, firstly the key columns are checked for brick or stone aggregate concrete. In case of unknown column material, brick aggregate is assumed. Due to the absence of any compressive strength data for existing RMG factory buildings, equivalent compressive (cylinder) concrete strengths (f?c) are used for preliminary analysis. For the key columns with stone aggregate concrete and brick aggregate concrete, equivalent compressive (cylinder) concrete strength (f?c) are assumed 16.3 MPa (2365 psi) and 14.1 MPa (2045 psi) respectively. These two equivalent concrete strengths were estimated on the basis of the cylinder test results conducted at BUET Concrete Laboratory between 2003 and 2009 using equation (2).
f ?c=Mean of concrete strengths -
1.34 x Standard deviation of concrete strengths (2)
After deciding on concrete strengths of the key columns, the order of reinforcement is checked with a ferroscanner to calculate the area of reinforcement (Ast). In case of unknown number of reinforcement bar, it is assumed 1% of gross area of concrete section. For the buildings constructed before 2005 and after 2005 the steel strengths (fy) are assumed 40 ksi (276 MPa) and 60 ksi (414 MPa) respectively. After deciding on all these information, Column Ultimate Strength is calculated.
Finally FOS is calculated from Column Ultimate Strength and Column Working Stress. Based on FOS, four color codes have been proposed to be used indicating the level of vulnerability of the factory buildings and the required actions within certain time frame to overcome the vulnerable condition. Table 1 shows the color codes based on FOS of columns along with required actions within time frame. Thus, preliminary assessment of immediate threat of collapse from current building use is carried out.
After each inspection, preliminary assessment reports are prepared including the findings along with required recommendations for the building owner and user according to the assessment results. After assessment if any factory building is notified as hazardous, the respective assessment teams let the review panel of Bangladesh government know about those factory buildings to carry on further assessment by inspection team and take final decision regarding the closure of the factory.
For factory buildings falling under red and amber category, Detailed Engineering Assessment (DEA) is carried out. Other issues triggering DEA are: concerns with structural issues, i.e. extensions, lateral system, flat plate punching capacity and slender columns, and state of documentation and approvals. DEA of the buildings involve soil investigation, other non-destructive tests and 3D building modeling.
Core tests are essential actions for factory buildings falling under red, amber and yellow category to gradually improve the state of building and reach to green category. For the purpose of core test at least four, three inch diameter core samples are required to be collected and tested and ACI 562 (2013) is used to estimate equivalent concrete strength from the core data.
TABLE I
COLOR CODES BASED ON FOS OF COLUMNS ALONG WITH REQUIRED ACTIONS WITHIN TIME FRAME STRUCTURAL ASSESSMENT OF BUILDINGS HOUSING RMG FACTORIES
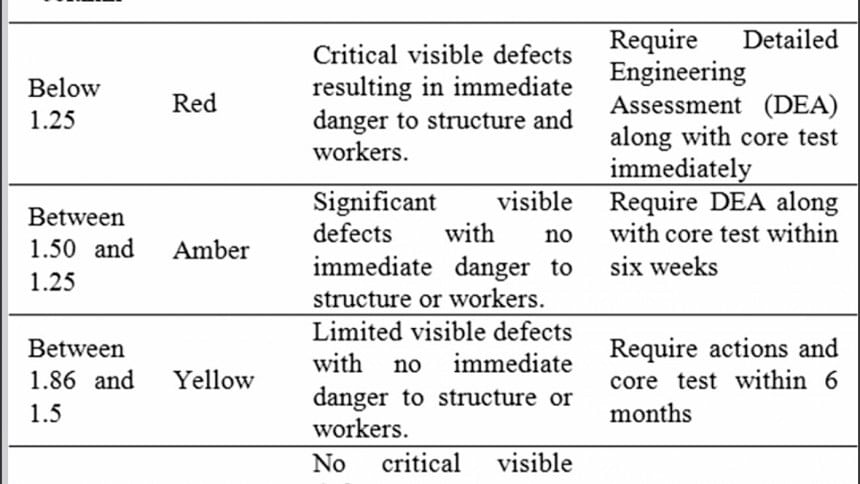
Findings from RMG Factory Buildings' Structural Assessments
Starting from June 2013 until February 2015, 4552 core samples of 825 factory buildings were collected and tested at BUET's Concrete Laboratory, among which 2673 samples are of brick aggregate and 1823 are of stone aggregate. Out of these 825 factory buildings, 12 are built before 1980, 198 are built between 1980 and 2000 and the rest after 2010. Approximately, 52% of those factory buildings are constructed after 2005. Figure 2 shows distribution of these core test results for all aggregates, stone aggregates and brick aggregates along with number of sample cores for the tests, and mean and standard deviation of strengths found from the tests. For overall all the aggregate samples, the mean and standard deviation of strength are 3009 psi (20.8 MPa) and 1290 psi (8.9 MPa) respectively. For brick aggregate sample cores, the mean and standard deviation of strength are 2805 psi (19.3 MPa) and 1231 psi (8.5 MPa) respectively. For stone aggregate sample cores, the mean and standard deviation of strength are 3312 psi (22.8 MPa) and 1320 psi (9.1 MPa) respectively.
Detail Engineering Assessment (DEA) is required to have in-depth understanding of the condition of the structure. It also identifies inadequate structural members (if any) with respect to capacity as per code. In addition to that the condition of the structure can be assessed for different loading conditions. As per Alliance, Accord, and NTC guideline (NTPA, 2013), DEA is required if the visual or initial assessment found structural distress in main load-carrying members, apparently inadequate main structural members for both vertical and lateral load, or extension beyond design drawing or permission. Accord and Alliance have published their own protocol regarding DEA. The typical Steps for the assessment are shown below. The steps may vary according to the level of assessment and information available.
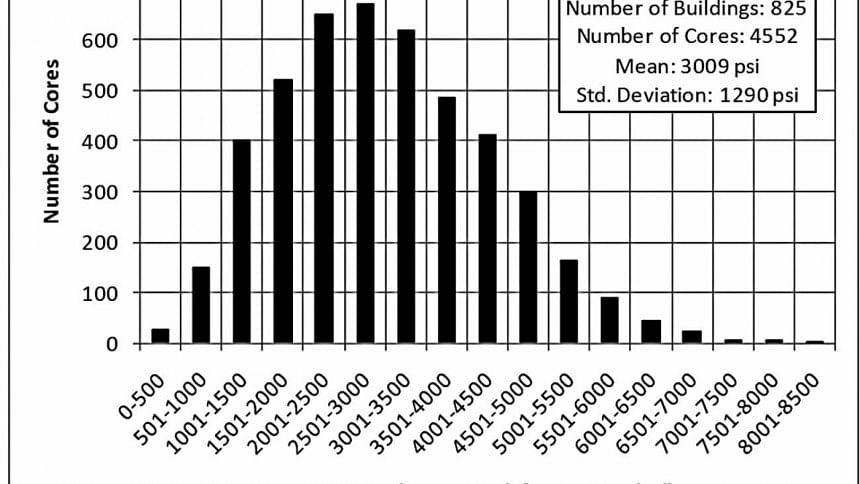
Prepare As-built Architectural and Structural drawings, if not available already. The as-built drawing shall show the structural, non-structural elements with dimensions at all levels, foundations and framing on plan, section and elevation, and cross-sectional drawings showing reinforcements in foundations, columns, beams, slabs etc. If as-built drawings are available - verify if it truly represents the structure. As-built drawing shall be prepared/ checked as per NTC Guideline (NTPA, 2013).
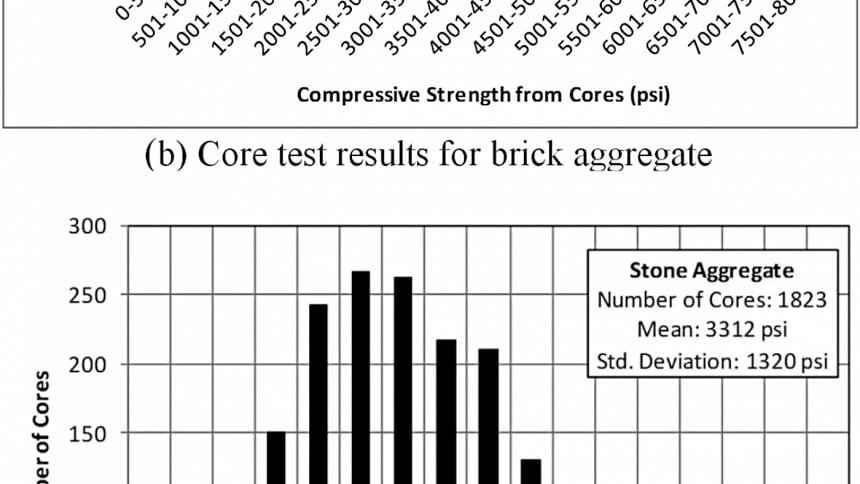
Scanning of reinforcement bars in main structural elements of lower tiers to confirm as-built condition.
Confirm bar size by drilling 50mmx 50mm holes at rebar location.
Arrange confirmatory soil test (2 to 3 borings).
Spot check of foundation by excavation, if necessary.
Identify causes of any physical distress, dampness or any other abnormalities and suggest remedial measures.
Work on specific items of concern identified in the initial structural assessment report
Identify any overloading, additions, extensions, presence of water tanks, towers. Study their effect on the structure and suggest remedial measures.
Arrange for core test by taking 4 Nos. 3 inch cores (preferably from columns) to assess in situ strength ensuring sample reliability, testing of cores in approved laboratories only, and proper interpretation of core test results considering various factors as per ASTM C42-90.
Use ACI 562 to find equivalent concrete strength to be used in design checking
UPV tests may also be conducted with proper calibration.
Prepare structural model as per As-built drawing using appropriate software by following the standard practice and building code.
Obtain reliable data on steel grade or arrange testing of steel rebar (if possible) or assume 40 grades conservatively for using in all analysis/design adequacies.
Use loading and Load factors as per standard (NTPA, 2013).
Check strength and serviceability requirements as per Bangladesh National Building Code (BNBC, 1993).
Make recommendation(s) based on results of DEA- including restriction of loading, restriction on vertical extension.
In case of deficiency in structural integrity of the structure(s), appropriate retrofitting scheme is to be designed.
Prepare Load Plan and arrange posting of load plan and approve it.
Submit report for review by the Engineering Team
Retrofitting is the modification of existing structures to make them more resistant and safe. In case of factory buildings, retrofitting will have to be carried out as per the DEA. The DEA of factory buildings will incorporate a full structural evaluation of the building, as well as investigation of ways to improve the factory buildings based on several defining criteria. In case of retrofitting, the requirements of BNBC are to be adhered to as much as possible, although it recognized that in some cases a fair judgment must be made as to how much a building can be improved based on its existing condition, as well as how economical it will be to satisfy every design criteria as stipulated by code requirements. The overall strategy will be generally as follows based on a hierarchical principle of increasing compromises:
a) Follow strictly the code design requirements to assess the actual deficiency of the building under analysis.
b) Determine all possible requirements, and which compliant factors can be relaxed in order to achieve a minimum level of compliance of another factor which does not comply (for example, the relaxation of floor loading in order to achieve a reasonable level of punching shear resistance when taking into account lateral loads which cause unbalanced forces within the structural system)
c) Propose a comprehensive remedial plan based on the extent of works and the practicality of carrying them out cost-effectively. Prepare alternative retrofitting schemes to remedy the structural deficiency. Discuss with the owner about construction issues and cost. Decide the most optimum retrofitting option.
d) Submit Retrofitting Scheme for review by the Assessment Team.
e) Supervise retrofitting work during construction for quality control and certify the structural integrity/safety after construction as per the provision of the Remediation and Oversight Protocol.
In some cases, situation may arise at which the results of the analysis may have the possibility of rendering certain buildings completely unfit for purpose, and the extent of remedial works may be too much and too complicated to implement. In such cases, it should be decided whether or not partial or complete demolition and reconstruction should be considered as a single viable option.
There is no denying that Bangladesh has progressed a lot since three years after Rana Plaza collapse in terms of achieving workplace safety compliance issues in RMG industry, under three plans of actions - National Tripartite Action Plan (NTPA), the European Union Sustainability Compact, and the United States Trade Representative (USTR) Plan of Action. Among 25 commitments under the National Tripartite Plan of Action on Fire Safety and Structural Integrity (NTPA), 16 have been fully or substantially completed and nine have been partly completed. Among a total of twenty nine listed activities in the EU Sustainability Compact, 15 actions have been fully or substantially completed, 13 actions have been partly completed, and one action regarding encourage retailers and brands to adopt and follow a unified factory audit code of conduct in Bangladesh has not been initiated yet. The United States Trade Representative (USTR) proposed a sixteen-point action plan, where substantial progress has been made in regards to twelve of the actions and greater progress is required in regards to four actions.
In all three plans of actions, structural assessments of buildings housing RMG factories have been given importance, with regard to which substantial progress has been made, i.e. up gradation of Chief Inspector of Factories and Establishment office to DIFE, sanction of 679 new staff positions including 392 new, organization of training program for capacity building of the newly recruited inspectors, development of Guidelines for Assessment of Structural Integrity and Fire and Safety including harmonized standards, establishment of a review panel along with a review mechanism to handle urgent safety issues in garment factories, initiation of assessments of the structural integrity and fire safety of RMG factory buildings, and creation of publicly accessible database of all RMG factories as a platform for reporting labour, fire and building inspections.
On the other hand, structural assessment alone is not enough to ensure a safe working environment for all in the sector. The weak factory buildings are required to be strengthened to ensure resilience through different initiatives, i.e. preparation on Corrective Action Plan based on the assessment findings, Detailed Engineering Assessment as proposed in the initial assessment report, and retrofitting as requirement. The Accord and the Alliance have showed much progress in preparation of CAP, but no CAP has been prepared under National Initiative so far. So, immediate actions are required by NTC to address the issues.
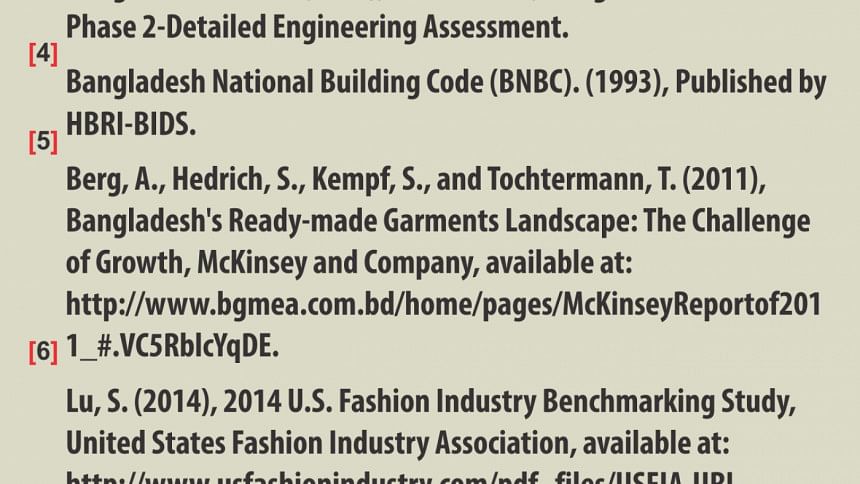
Comments