'Greening' the RMG sector

A study recently presented at a dialogue was titled "Environmental compliance opportunities in the Bangladeshi readymade garments industry: Lessons from the green high-achievers," which called for reviewing policies about institutional structures around environment and water quality. The event was co-hosted by Adam Smith International, MCCI, UK Aid and the Economic Dialogue on Green Growth. The executive director of the Centre for Policy Dialogue (CPD) stressed on the fact that factories need to voluntarily adopt green measures which would lead to "sustainable development of RMG industry."
Opinions are divided on whether it is a viable option for manufacturers to go "green" because of the finances involved in the "greening" process. The general argument against going green that is being touted by the majority of manufacturers (who haven't gone green) is that buyers are not willing to pay more for the substantial investments involved. The counter-argument to that point of view is that Bangladesh already has many LEED-certified factories. LEED stands for "Leadership in Energy and Environmental Design"—a certification from the US Green Building Council (USGBC). If we look at the data available from BGMEA, of the top 10 LEED-certified factories in the world, seven are from Bangladesh. All seven are "Platinum" rated, which is the highest category that can be reached under this globally recognised certification. Twenty factories are in the LEED Platinum category and 40 are in LEED Gold. Indeed, there are 73 Bangladeshi LEED Green garment factories certified by the USGBC. There are some 320 factories in the pipeline waiting for LEED certification. Hence, the argument that LEED certification doesn't pay isn't exactly correct.
So why are the major players going green if it doesn't pay? The greening process starts from scratch for those RMG manufacturers who have foresight. For instance, some companies are setting up facilities taking into consideration that it makes sense to design the physical infrastructure in a manner that would make less demand for power, with more provisions for natural light to permeate into the plant/office space (meaning less money spent on electricity bills). Water consumption is regulated, and catching and storing natural rainwater by allowing it to soak into the ground to replenish underwater tables is part of the "green" way of doing things. Harvesting rainwater (which doesn't cost factories much) is another way to save on water.
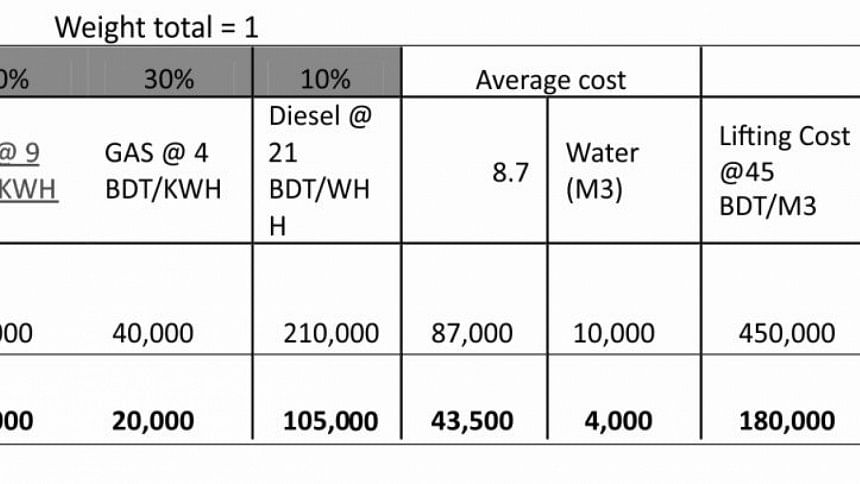
Now, concerning the actual plant itself, technology is already there that makes use of highly efficient LED lamps, which are touted to be around five times as efficient as CFLs, which in turn are three times as efficient as normal tube lights. Some manufacturers are decommissioning older clutch and plate motor machines and replacing them with energy efficient direct drive and servo motor-driven machines. Yes, there are costs involved, but if we look at the savings in energy bills, it all makes sense. The other thing that LEED-certified manufacturers are putting into place is sensors that automatically monitor lighting levels—another piece of proven technology used in abundance in more advanced economies, as it takes out the human element and utilises artificial intelligence to make optimal use of lights as and when needed. We even find solar power being used to save on conventional energy, which is becoming more and more expensive with each passing year. Hence, how we design our factories is of prime importance because substantial savings can be made in water and energy consumption.
Green factories are increasingly making use of green grass and other vegetation. It is not merely for beautification purposes; rather, there is an environmental aspect to it. Extensive use of canopied trees covering the landscape of factories can effectively reduce heat levels which help reduce the usage of air conditioners and that in turn reduces GHG emissions.
The philosophy governing "going green" is to introduce environmentally sustainable manufacturing. Being environmentally conscious actually makes good business sense. Some factories in Bangladesh which have embraced this philosophy boast savings of up to 65 percent in water usage, more than 40 percent reduction in CO2 emissions, and 40-50 percent reduction in electricity consumption. Those are serious figures which can be translated into takas and paisas. The Table 1 example is based on the energy and water scenario. Grid electricity is supplied by REB and the factories use natural gas and diesel to generate their own electricity, as back up, when grid supply is disrupted. As we can see, green factories are substantially more cost-efficient than those that are not green.
Now, if we look at Figure 1, we can see the progression of a factory going green over a period of three years where the cumulative effect of introducing "efficient" machines and improved building design has a two-fold effect: production output increases whilst consumption of production variables like water and energy consumption comes down.
Figure 1 is an example of a knitwear production LEED Platinum facility. For instance, production increases from 6 million pieces of knitwear garments in 2015 to 7 million in 2016 and then to 8.8 million pieces in 2017. So production increase in 2016 (over 2015) was 17 percent, and in 2017, it further increased by nearly 26 percent over the preceding year. Now, here's the catch. When we look at consumables, i.e. water and energy, those inputs actually decreased over the same period. From 2015 to 2017, water consumption came down from 0.15 M3/KG (cubic metre of water/per KG of knitwear) to 0.11 M3/KG. Similarly, energy consumption came down from 1.84 KWH/KG (kilowatt hour per KG) of knitwear in 2015 to 1.57 in 2017.
The anxiety that many manufacturers in Bangladesh are suffering from is how they are going to recoup costs by investing in green technology. By greening their factories, they are going to intiate significant cost savings in water and energy, which translates into monetary savings, while at the same time, the introduction of new technology will increase production output. Another point that the manufacturers should keep in mind is that there is such a thing as "ethical buying"—and buyers falling into this category serve a customer base which is very conscious about under what conditions their products are made. In that sense, green factories have a natural advantage over those that are not green. At the end of the day, we need the RMG sector to take responsibility for the environment, and greening of factories, if done right, makes good business sense too.
Syed Mansur Hashim is Assistant Editor,
The Daily Star.
Comments