Takeaways from 2021 and prospects of 2022
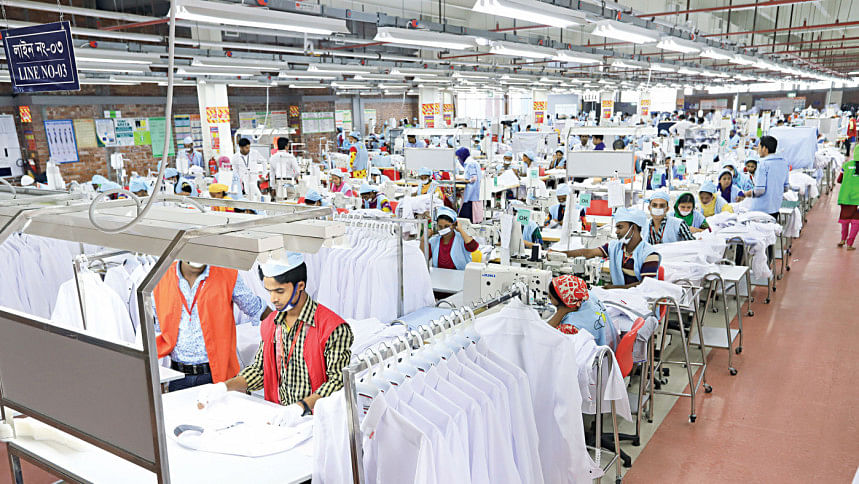
The year 2021 started with a hope to overcome the crisis caused by the coronavirus pandemic and rebuild the industry. With many momentous changes that happened throughout the year, it was a year of challenges and turnaround, yet a significant moment to transit to the next phase of development.
Our sincere gratitude to Honourable Prime Minister Sheikh Hasina and her government for the unprecedented support that kept the industry on course indeed.
We are still on the recovery phase and export is gradually picking up as the recent trend shows. Concern is looming around the spread of the Omicron variant and how it may affect our market and the turnaround we have made so far.
Maintaining a balance between lives and livelihood was the biggest challenge for the industry during the pandemic. But we proved our resilience by continuing our operations through maintaining stringent health protocol in the factory.
The vaccination brought a new hope as global economy saw sharp uptick in its recovery, yet we had to face the aftershock of the crisis. The sourcing pattern was disrupted as buyers opted for smaller orders with speedy delivery.
Global freight management system is severely disrupted pushing the container freight cost up by 350 per cent to 500 per cent. Prices of cotton, yearn, fuel, dyes and chemicals went up, causing significant cost burden to manufacturers who were already struggling.
The near-shoring tendency among the buyers to minimise the freight costs is also being observed during this time. While these all are matters of concern for us, we learned about the inherent vulnerability of this industry that emerged from the weakness of contracts and trade term, lack of raw material supply from local sources and overdependence on a few countries, and the economic security of the workers in a pandemic like situation.
Covid-19 has taught us the importance of deepening buyers-suppliers relationship more than ever before. As we do business based on the account receivables, so there is always a risk of order cancellation, delayed payment or violation of trading terms of some sort.
The pandemic also unveiled new opportunities for us. Global online sales have gone up astronomically during this period with the emergence of technologies, disrupting the retail industry to a significant extent.
Considering the importance of the digital marketplace, the BGMEA has undertaken a research project that will assess the feasibility of Bangladesh's RMG industry and its readiness along with policy priorities entering into the virtual marketplace.
In just about five years, our personal protective equipment (PPE) export has grown from $252 million to $618 million in FY2020-21, as per data of the Export Promotion Bureau.
Bangladesh's export of textile face masks without a replaceable filter or mechanical parts, including surgical masks and disposable face masks of non-woven textiles was worth $105 million in 2020-21, which was only $0.46 million in 2014-15. So, considering the global demand and the rise in demand for PPEs in post-Covid reality, we have a clear potential to tap into it.
But there is certain hindrance that needs to be taken care at first. Particularly, medical grade PPEs would require significant capacity building within the industry that requires policy supports.
With 153 LEED-certified factories, Bangladesh is now home to the highest number of green garment factories in the world. The BGMEA received the "2021 USGBC Leadership Award" for its exemplary leadership in promoting environmental sustainability and green industrialisation in the RMG industry. The BGMEA joined the UN Fashion Industry Charter with an ambition to reduce GHG emissions by 30 per cent within 2030.
The industry has positioned itself as one of the most responsible manufacturing undertakings in the world. In recognition of our efforts, the Hong Kong-based ethical audit firm QIMA placed Bangladesh second in the global ethical manufacturing ranking.
Going forward, we have to continue all of these transformations and momentum that we have achieved.
Most importantly, we need to redefine our business model. If we can't upgrade the business capabilities and value addition of the industry, the achievements in environmental and social fronts will be uncertain. So, our priorities in the coming days will be to transform our business model - from labour-intensive manufacturing to innovation, high-value addition, and modern manufacturing processes.
With only a 6.26 per cent share in the global market (as per the WTO data in 2020), Bangladesh has huge untapped potential. Though in the last fiscal year, the export growth was comparatively lower, we believe that by the end of 2021 our share will reach around 7 per cent, and in 2022 it will surpass that level.
Achieving excellence in products, fibre, and markets diversification and value addition are the key opportunities for this sector. For that, we have to build our capacity of the backward linkage industry.
As Bangladesh has graduated from the least-developed countries' category, there will be certain changes in the global trading rules. To comply with double transformation rules of origin after 2026, there is no alternative to increase investment in the backward linkage industry.
Within the textile sector, there is a largely unexplored area highly potential for investment, which is the man-made fibre-based yarns and fabrics, functional fabrics like polyester, viscose, spandex, mélange, etc.
Globally the share of cotton textile and clothing consumption is 25 per cent only, whereas 75 per cent of Bangladesh's RMG product is concentrated within cotton items. So, huge scope and opportunity are awaiting us.
We do also have a capacity shortage in the area of high-end garments like sportswear, lingerie, outerwear, etc. where we have a huge market, but insignificant presence. For the transformation to a high-end industry, we do also need specialised investments at this moment, for example, in a product category like shirting fabric, laces, hooks, etc. There is a persisting shortage in supply of this kind of raw materials where we need investments.
For us, the path is to graduate from OEM (Original Equipment Manufacturer) to ODM (Original Design Manufacturer) as we focus more on design development, innovation, and end-to-end digital manufacturing. So, we need investments to upscale our capability in innovation and adaptation in the area of design as well as to cope up with the fourth industrial revolution.
To make our supply chain lean and green, we need to ensure technological up-gradation across the production chain, otherwise, it will be difficult for us to optimise cost and be competitive in the global market.
We will have to approach newer avenues of cost optimisation and being efficient, including industrial engineering and lean manufacturing, production planning, and supply chain management. Our success will depend mainly on developing the skills and efficiency of our people.
Investment in the area of re-skilling and up-skilling our workers is important to take the advantage of the fourth industrial revolution. Since human resource is the main strength of this industry, so ensuring their safety and well-being will be the main priority.
Keeping in mind the need of the time, the BGMEA is setting up the "Centre for Innovation, Efficiency and OSH" on its premises. The centre is expected to come in to operation in early 2022. Through this centre, we will focus on newer avenues of enhancing our competitiveness through efficiency improvement and cost optimisation.
We will also work to facilitate automation, 3D designing, innovation, using best industrial engineering process and practices, enlighten on end-to-end digital manufacturing and inspire modular processes.
There is no doubt that Bangladesh is going forward with tremendous progress where the contribution of the readymade garments industry is significant. Over the 40 years journey, the RMG industry of Bangladesh has passed so many crossroads and Covid-19 is another big obstacle.
To overcome the challenges posed by the pandemic and provide a clear direction towards sustainable development, a strategic roadmap for this sector is warranted.
Though we have the opportunities and challenges are well identified, the recovery from Covid-19 is yet to see solid progress. A good number of European countries have already imposed restrictions to contain the fourth or fifth wave. So, 2022 seems to be quite uncertain.
We need to be prepared to face any shock, continue our efforts to maintain health protocols and follow a cautious step to plan our capacity, supply chain management and future expansion.
The author is president of the Bangladesh Garment Manufacturers and Exporters Association.
Comments