Ceramic factories in north struggle for survival
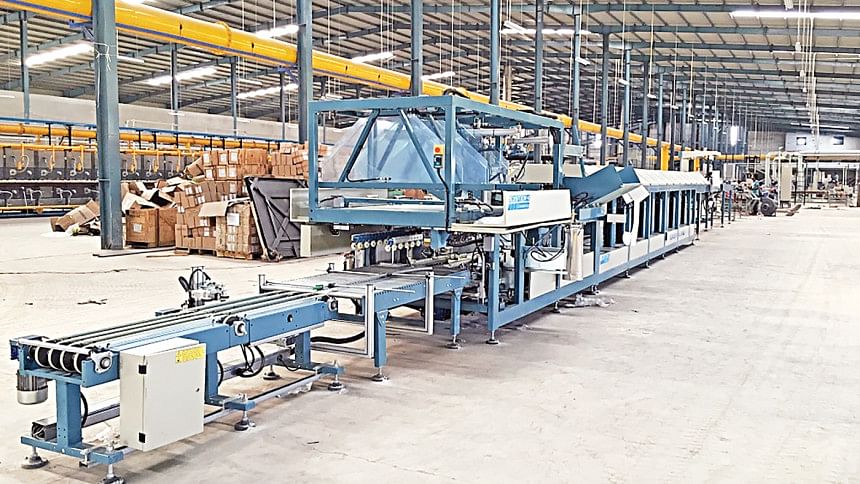
Ceramic factories in underdeveloped regions of northern Bangladesh are struggling for survival as other than absence of natural gas, the ongoing US dollar crisis has led to a roughly 40 to 50 per cent increase in production costs.
This is because the required raw materials are not being imported as per the needs of ceramic makers, who are facing difficulty in opening letters of credit amid the US dollar crunch, according to industry people.
Besides, the unavailability of natural gas means local entrepreneurs have to adopt innovative but expensive means of collecting alternate fuels to run their units. This includes burning coal and even waste tyres to produce ceramics.
There are four ceramic factories in greater Rangpur with three based in Nilpamari -- Sanita Ceramics (Pvt) Ltd, Glory Ceramics (Pvt) Ltd andSanita Tiles (Pvt) Ltd -- while Apple Ceramics (Pvt) Ltd is situated in Rangpur.
Excluding Sanita Tiles, the rest of these units mainly produce sanitaryware.
Sources say that due to the US dollar crisis, imports of key raw materials such as china clay and ball clay have significantly fallen this year.
As per data from the National Board of Revenue, combined imports of china clay and ball clay fell to 9.86 lakh tonnes in the July-April period of the current fiscal, down by some 16 per cent from 11.81 lakh tonnes the previous year.
Shipments of other raw materials, including quartz stone powder, felspar, calcium carbonate, zinc oxide and barium, also witnessed a declining trend.
Samiul Islam Shawon, managing director of Sanita Ceramics, said the first step to produce ceramics requires mixing various ingredients before melting them at a constant heat of 1,200 degree Celsius.
Any fluctuations in temperature during the melting process would hamper the quality of finished goods and so, natural gas is a cost-effective means of sustaining steady heat.
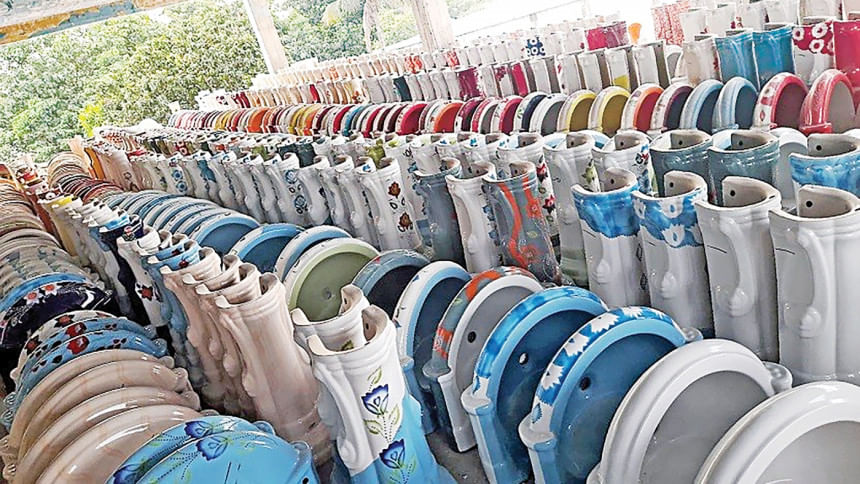
"But we are still deprived of natural gas and struggle to arrange alternative fuels to run operations," he added.
Shawon went on to say that they burn coal to generate gas for getting the required heat for melting raw materials in a furnace at their small unit.
However, this is very costly as the price of coal recently shot up to Tk 20,000 per tonne while it was Tk 7,000 last year, he said.
Md Zikrul Huque, chairman of Glory Ceramics, said they are using pyrolysis oil to substitute natural gas at their factory.
Pyrolysis oil is made by burning waste tyres in a specialised plant.
However, this increased the production cost by 25 per cent compared to natural gas.
Besides, the US dollar price is too high now and the assessment value of customs risen as a result, making the price of imported raw materials rise by 34 to 37 per cent.
"In this situation, our production has fallen by 40 to 50 per cent even though in usual time we have the capacity to meet the need of quality sanitary goods in local markets," Huque added.
Mozahedul Islam Faruque, chairman of Sanita Tiles, said the government should exempt them from the 15 per cent supplementary tax on the production of tiles as it is not a luxury item.
Considering the adverse reality, the Bangladesh Ceramic Manufacturers and Exporter Association (BCMEA) has been demanding as such for a long time, he added.
Sirazul Islam Molla, president of the BCMEA, said taxes on imports of clay should be calculated based on their actual weight as much of these materials are bloated with water when they arrive.
"If all drawbacks are solved, tiles made in Bangladesh could be exported as we produce quality goods," he added.
Just two decades ago, the country's demand for ceramic goods was largely met through imports. Now though, the scenario has changed as new factories are being set up with local production catering to 86 per cent of the market worth some Tk 7,250 crore.
Of the 70 ceramic factories in Bangladesh, 32 produces tiles, 20 make tableware and 18 provide sanitary goods.
Comments