Top cement makers shifting to eco-friendly production
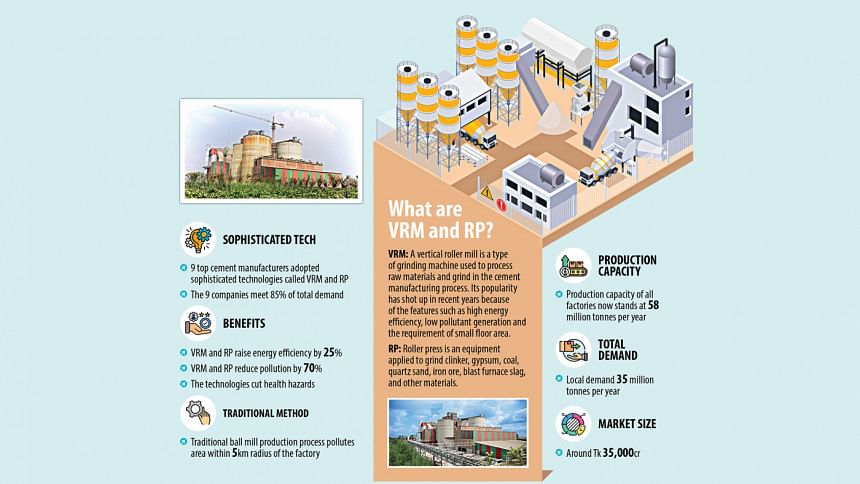
Bangladesh's major cement manufacturers are increasingly shifting to eco-friendly production processes with a view to cutting energy consumption and pollution and ensuring the sustainability of their business in a world that is getting more worried about industries' carbon footprint.
As part of their green transformation, the mills have replaced their traditional ball mills (TBMs) with sophisticated vertical roller mill (VRM) and roller press (RP) equipment, industry people said.
The roller press is an equipment applied to grind clinker, gypsum, coal, quartz sand, iron ore, blast furnace slag, and other materials.
A VRM is also a grinding machine used to process raw materials. Its popularity has shot up in recent years as it is energy efficient, emits a low level of pollutants and requires a small floor area.
According to local manufacturers, although VRM and RP-based manufacturing lines are three times costlier than the traditional ones, advanced technologies can help sustain businesses in the long run.
Nine large companies -- Shah Cement, Bashundhara, Fresh, Premier, Seven Rings, Crown, LafargeHolcim, HeidelbergCement, and Akij Cement -- that collectively control 85 percent of the domestic cement market have shifted to the sophisticated manufacturing process.
"VRM and RP-based production processes reduce energy consumption by 25 percent," said Mohammed Amirul Haque, managing director of Premier Cement.
"At the same time, they are environment-friendly and cut pollution by around 70 percent compared to the traditional production line," he said, adding that developed countries have switched to VRM and RP a long ago.
Premier Cement's three production units, which have a combined daily capacity of producing 26,000 tonnes of cement, have shifted to the VRM system.
In Bangladesh, there are 37 active cement factories, with a total annual production capacity of 58 million tonnes against a demand of 35 million tonnes.
Haque claimed the RP-based system is cheaper than the VRM-based ones, but their eco-friendliness and energy efficiency levels are almost the same.
He said VRMs generally have a higher grinding efficiency compared to traditional ball mills.
However, he pointed out that there is a shortage of technicians and engineers needed to maintain the VRM and RP-based production lines and repair the equipment used.
"So, we need to hire experts from the European countries that also supply the equipment."
Md Moshiur Rahman, head of business (marketing) at Akij Cement, says VRM and RP are eco-friendly but costly.
VRMs can, however, lead to lower operating costs over the long term thanks to their energy efficiency and reduced maintenance requirements, he said.
The cement industry is one of the major sectors responsible for huge carbon emissions and air pollution, not just in Bangladesh, but also across the world.
So, the initiative of the local cement manufacturers will help them to be compliant and become a part of the global commitment aiming at reducing carbon emissions and air pollution, said Fahmida Khatun, executive director of the Centre for Policy Dialogue, a think-tank.
"Advanced technologies will help the industry reduce health hazards and improve efficiency. In the long run, entrepreneurs will benefit thanks to their adherence to compliance and a cut in the cost of production."
"Even green technologies will contribute to cement exports in the future."
Crown Cement has installed VRM in its fifth production line to increase cost efficiency and make the production process more eco-friendly.
The sixth unit, which is expected to start its operation by this year, will also be VRM-based, said Md Mozharul Islam, company secretary of Crown Cement.
Prof Ahmad Kamruzzaman Majumder, chairman of the Department of Environment Science at Stamford University, said a TBM-based cement factory pollutes areas located within the 5-kilometre radius of the facility.
Air pollution caused by cement factories also creates health hazards for workers as well as the people living in the surrounding community during the manufacturing, loading and unloading of raw materials and finished goods, he said.
Thanks to the installation of VRMs and RPs, factories can control pollution inside the facilities but it might not be easy to curb the pollution brought about by the entire supply chain, according to Majumder.
Prof Majumder said they would complete a study within a short time to find out how much pollution will remain despite the adoption of modern technologies.
Comments