Precast and Place-Cast Concrete
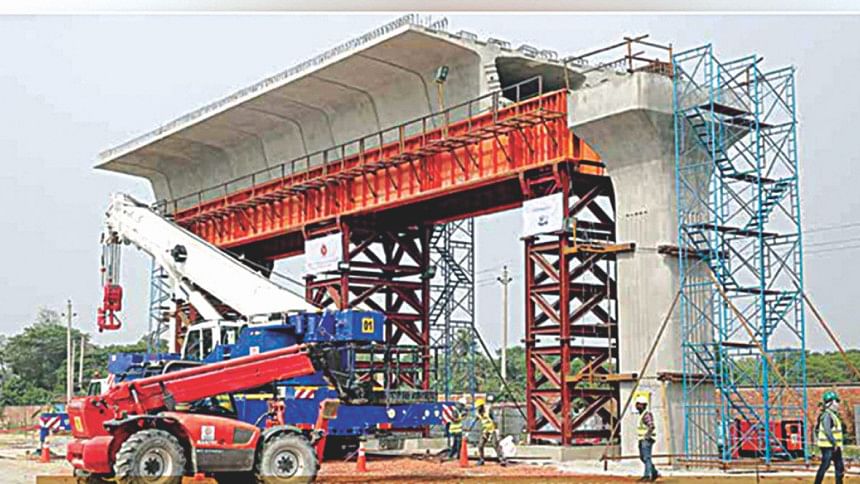
Concrete is the second most consumed material in the world after water. It is estimated that every year 21 billion tonnes of concrete are consumed globally by 7 billion people. This large volume of concrete is used for making buildings, bridges, tunnels, roads, ports, and other infrastructures. Based on the place of casting, concrete is divided into place-cast or cast-in-place or cast-in-situ concrete and precast concrete.
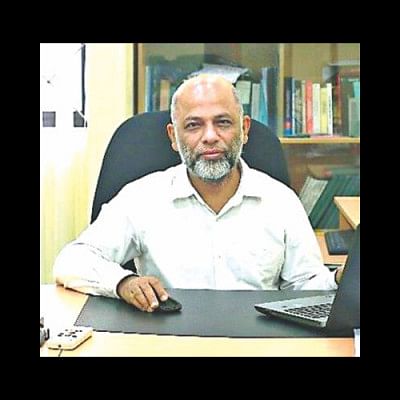
During construction, site-specific forms are made and then concrete is poured into these forms to give the shape of the structural elements. This traditional technique of concreting at place is called place-cast concrete. On the other hand, structural elements can be fabricated at a factory or a construction yard and then transported to the construction site after adequate curing. This technique of offsite production of concrete is called precast concrete. Because of bad weather, it is very difficult to control overall quality of place-cast concrete. Moreover, bad weather delays the schedule of the project and results in additional costs to the project. Precast concrete eliminates these problems as it is manufactured in a controlled environment, ensuring extreme accuracy in quality, strength, and fine aesthetics. Due to these various advantages of precast concrete over place-cast concrete, the consumption of precast concrete is increasing globally. It is expected that the global precast concrete market will be worth USD 150 billion by 2025 with a growth rate of about 6 percent. The following advantages of precast concrete can be noted over place-cast concrete:
* Precast concrete is manufactured in a controlled factory environment. Therefore, the desired quality of concrete can be achieved.
* As the production of structural members is replicated in precast industries, the cost is reduced.
* Bad weather may hamper time schedule and quality of place-cast concrete.
* Less amount of labour is required in precast concrete. More skilled labour is required in place-cast concrete.
* Precast members can be installed immediately after delivery at the site. There is no waiting time at site.
* Due to the repeatability of precast production, it's easy to make many copies of the same product. By maximising repetition, it is possible to get plenty of value from a mold and a set-up.
* In precast concrete, accelerated curing to get strength early (even by several hours) is possible by increasing temperature and maintaining sufficient humidity.
* The precast elements can be produced with the desired shape, surface finish and texture with accuracy.
* The precast structures can be dismantled, when required, and they can then be suitably reused elsewhere.
* The transport and storage of various ingredients of concrete for place-cast concrete work are eliminated when precast members are adopted.
* The amount of scaffolding and formwork is considerably reduced in precast concrete.
* In precast concrete, due to the controlled nature—from materials to consolidation to curing—it is possible to make extremely durable concrete. The waste of materials will also be reduced in precast concrete. These will certainly help toward sustainability of construction materials.
The following disadvantages of precast concrete can also be noted over place-cast concrete:
* The precast elements may be damaged during transport, if not handled properly.
* It is difficult to produce satisfactory monolithic connections between the precast members.
* It is necessary to arrange for special equipment and vehicles for lifting and moving the precast units.
* The economy achieved in precast construction is partially balanced by the amount to be spent in transport and handling of precast members. It therefore becomes necessary to locate the precast factory at such a place that transport and handling charges can be brought down to a minimum.
Rise in population, rapid urbanisation, and robust economic growth are the major macroeconomic drivers of the precast construction market in Bangladesh. However, high initial cost and logistical and material handling damages are anticipated to be the challenges for the growth of this market in Bangladesh.
Dr Md Tarek Uddin, PEng. is Professor, Department of Civil and Environmental Engineering (CEE), Islamic University of Technology (IUT).
Comments