Fabrics of Heritage
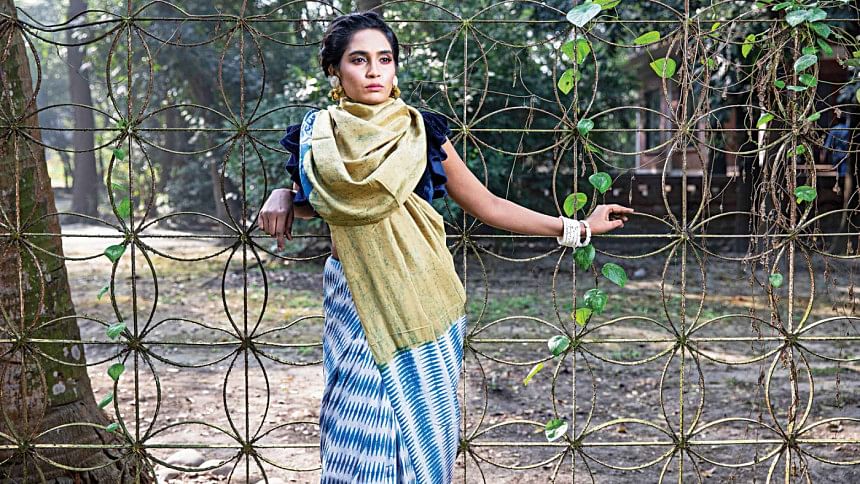
Farfetched as it may sound, this is the truth — this is history. Eventually with time, our grandeur subsided. Maybe there were forces acting against us or maybe it was our own short-sightedness that led to the demise of an incredible craft.
However, today, a few centuries later, in a sovereign Bangladesh we are trying to build a link with our lost heritage. With the announcement of GI (Geographical Indication) for Jamdani — that it is our own, the announcement that Sonargaon be considered as World Craft City by The World Craft Council and the intense research into reviving the wonder cotton — karpash, we are getting closer to the idea, of reviving a lost culture. But can we say the same about all the other textiles that also took a part in writing the story of our nation?
What about the Tangail taant or even the Rajshahi silk?
Here, in this article, which has been divided in a three-part series, we delve into the lives of the fabric artisans throughout our nation. Trying to understand the standpoint of heritage fabrics in today's Bangladesh. Where the country has been successful and where it is on the verge of trailing behind.
The magnificence of the nakshi kantha
On the way to the borders of Meghalaya from Dhaka, we are faced with miles of scenery within the national borders. With small hills and forests filled with timber, the depiction is close to the definition of tranquillity. Amidst these very green laden forests are tiny mud huts and modest single storied brick houses where the women are busy taking care of their families.
It's a typical lifestyle for these women from the Jamalpur and Sherpur region, except for the fact they are also regarded as a national asset with their exceptional talent in crafting art such as Nakshi Kantha, on a daily basis.
Daluara Begum, proprietor of Dipto Kuthir in Jamalpur Sadar, used to be one of these ladies. Today, she runs an industry providing employment opportunities to other people, both female and male, in her area. Begum gets excited upon meeting us and proudly shows us all her trophies, especially the one she was personally gifted by the Prime Minister.
She speaks of a brighter future, especially with the establishment of the proposed Sheikh Hasina Nakshipalli project, in Jamalpur involving an expansive budget of Tk 722 crores. According to the Bangladesh Bureau of Statistics (BBS) there are some 261 handloom families living in Jamalpur and Sherpur districts while there are also some 76 Nakshi entrepreneurs and 3,985 Nakshi artists in Sherpur only.
And this very project approved by ECNEC with a possibility of 1st phase completion by December 2021 will further patronise the crafts and encourage more to join the trade. In an era when handicrafts are valued globally and many countries of the world are using handicrafts as one of their main items of trade, this is certainly a valuable move that sees a profitable future.
Nargis Khatun from Krishno Nagar, Jessore agreed. "I got involved with the trade because of my mother. I learnt the craft and the fine skills from her and today, I take pride in training other girls, get involved with Nakshi, as it brings prosperity and pride to those who know the craft. There are so many girls who work under me today. I just give them the tracing, the fabric and the matched thread and they do the fine work," said Khatun.
Upon further discussion Khatun opened up to this correspondent that once upon a time, especially at the beginning when women started doing the Nakshi business, the men were slightly sceptical because of existent, and archaic culture of patriarchy.
"But things have changed today," said Khatun adding on to depict a clearer picture, "Today, the men of the households encourage their ladies to do such kind of crafts because they can easily do it, while staying at home – and do not need to go out of their houses. Additionally, it also brings in extra money allowing the women to make economical contributions in their 'united household' income," said Khatun.
Upon inspection we discovered that each Nakshi artisan earned around, Tk 4000-5000 per month on an average in a good month, and around Tk 2000-3000 when the sales were low. And additionally, with the Nakshipalli to be set in motion, things were about to get better for the residents of the region.
Maybe with increased patronisation from our end, we might one day be able to finally give the Nakshi its due respect and the fame that it deserves.
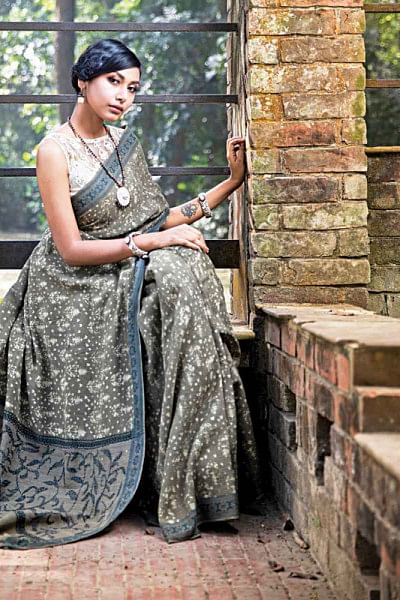
On the trails of the Rajshahi silk
Strolling down 2/7 Sir Syed Road, it is hard to overlook the antiquated silk shop that goes by the name of M/S Mollah Silk. The marquee silently beckons every passer-by to get inside and explore, and thankfully we had done the same because once inside we met the man who had built the organisation from scratch. The proprietor of the shop, Mohammad Safiul Islam was getting ready to call it a day, when we met him with myriad questions related to the famous Rajshahi silk. What came about from our conversations was completely unanticipated.
Islam had entered the silk trade back in the early '80s, along with his friend, Taimur, who was already settled in the trade. Originally hailing from Chapainawabganj, this was an industry that Islam had seen thrive right in front of his eyes. And naturally he became interested in the business.
"Everything was going well till the early '90s, when the then government removed the imposed 30 percent import tax on Chinese silk. The imported fabric was already subsidised by the Chinese government and a further deduction of import tax made it more lucrative to the traders compared to local silk.
"Pure, deshi silk failed to compete and businessmen eventually lost interest because customers became more inclined towards the foreign material," revealed the businessman.
What came about was a plethora of obstacles in the years to come, as farmers rearing the Silk Moth – bolur chaash, stopped producing it, and replaced the mulberry trees –tuunt gach — used to feed the moth, with mango trees instead, as they were much more profitable.
"Yes, those were the dark days for the Rajshahi silk industry, when production declined drastically. That's the time when businessmen including myself, shifted completely towards the Chinese variant of the thread, which is smoother — being machine produced. With those thread we used to make handloom fabrics and supply it to big organisations like Aarong, Aranya Crafts, Kumudini etc., even the businessmen residing in Sadarghat used to procure 1000s of meters of our handmade fabric to make panjabi and fatua and supply it to the rest of the nation," said Islam.
To the reader, this might seem to be a gloomy revelation, to know that the silk saris proclaimed to be pure Rajshahi silk, are actually spun with Chinese silk, but they are still handloom. Sadly, the confessions do not end right there, because according to Islam, even this format of survival, by the silk artisans of our nation, discontinued.
Today, there's a cheaper synthetic copy of the thread, imported from a neighbouring country that is way below the price of the Chinese variant.
"The synthetic variant is termed as 'reshom' in our country," said Islam. He added on to explain, "It is nothing close to the original reshom, but is a cheaper copy that customers find affordable." And with a syndicate playing with the prices of the Chinese thread, we are all at crossroads and nothing else.
"A 1 kg thread costs around Tk 5000-6000 which makes it Tk 500per yard and at retail price it goes around Tk 600-680 (balaka silk), additionally that means the cost price for a single panjabi would be something close to Tk 2000-3000, while with the cheaper reshom variants, an average panjabi can be made within Tk 500-600, which can easily be sold in the market at Tk 1000-1500 retail rate. How can we ever compete with that?" questioned Islam.
During our rendezvous, we also learned that the government'ssericulture board was operating at a much smaller scale than anticipated, rearing the Bombyx-Mori, (the scientific name for the silk moth) at a limited quantity. But according to the veteran silk enthusiast and trader, there was a lot of opportunity to contribute and help revive the industry.
"To encourage revival of the lost industry, the government can grow tuunt gach on its khaas lands, helping to revive the bolur chaash culture as a primary step to revival and then it can train the new generation artisans with the knowledge of silk-making process from the still existent experts in the field," said Islam.
And right he was, for this is a creative job that requires finesse, where the knowledge of the craftsmanship can only be passed down from the master craftsman to his apprentice. And this culture has already stopped for a long time now. To revive— it would mean learning the trade from the still surviving artisans and if they are all gone then it will only be 'too late' to turn back.
Islam concluded with few haunting words, "You can't blame the artisans from leaving their traditional job. Every other job including a rickshaw puller's pay around Tk 500 for a day's work (mojuri) and our artisans don't even get that. If we cannot value their gift, why will they stay?" he said, in a regretful tone.
The explanation was heartfelt and logical, on the other hand the benefits of reviving the industry also pose to be extremely lucrative, because that would mean, traditional silk artisans from the Rajshahi belt, including those who were involved with the sericulture, mulberry tree rearing etc., would get an opportunity to earn their living via an age-old method that was unique to the culture of their region, and we as a nation would earn the pride of wearing our nation's 'very own silk' and maybe even export it to other nations.
Not imported, not mill processed but made with pure 'khat khati kath' as the experts call it. Pure, handcrafted, Rajshahi silk, made with pure love and excellent craftsmanship of the skilled artisans of Bangladesh— almost as valuable as gold, if not more!
Photo: Sazzad Ibne Sayed
Model: Nobel
Wardrobe: Vegetable dyed silk from Aranya
Blouse: Zabin Iqbal
Make-up: Md. Hossen
Hair: Gazi
Styling: Zabin Iqbal
Location: Bengal Carpet Mill, Ford Nagar, Dhamrai
Comments