Fabrics of Heritage III
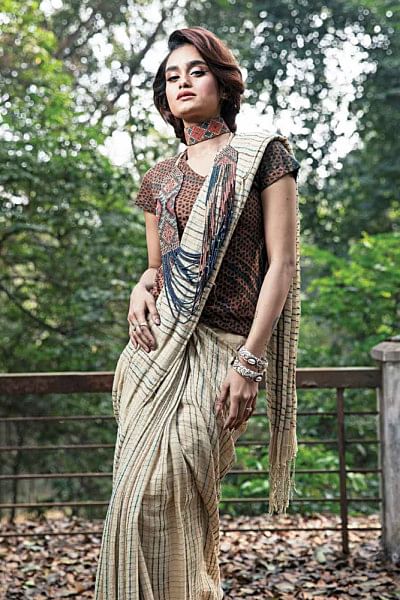
Transcribed through time – the Khadi
History reminds us that this method worked in motivating the locals. Everyone wore khadi dhoti, sari and handloom cotton products to lead their daily lives and ultimately nationalistic attitude took over.
Pradeep Kumar Raha, or as people lovingly call him — Kanti, took us a few years ahead of the colonial period.
Fast forward to the independence of Bangladesh. "Around the year 1972, I got involved with the trade that my father began in 1948. I was then a young master's graduate, with the dreams of changing the world. My thoughts were completely pre-occupied with our familial business and taking the trade to greater heights," Kanti opened up.
Based on Kanti's depiction of history, a milieu of khadi artisans propagated with titles such as Jogi Sampradaya and Katuni Sampradaya, involved with the craft itself and the thread making process, respectively.
"After the independence of Bangladesh, both the categories of artisans used to make the khadi chador, which was seasonal and mostly worn during winter. At other times, they did not have any work or did something else to earn a living.
This is when I thought of bringing a big change in the industry; a new, sovereign nation needed its own textiles to be truly self-reliant. And luckily, somehow, I got a contact from the then military — the BMA, to make monogrammed bed sheets and curtains for them. After that I got countless private orders for a similar service and the business took shape," recalled Kanti.
Based on the veteran textile connoisseur, Khadi has a lot of opportunities, especially if considered for the export market.
"Khadi can be diversified and made into so many different products. All we need at the moment is representation, marketing and patronisation of the root level artisans. Because if the latter is gone, then we will have nothing but a dead industry," said Kanti.
Kanti opened up with a heavy heart. "I could have left the country right at the beginning, I had all the opportunity to do so, but being a devotee of my home country, I stayed back. I tried my best to fight for my country in my own way, fight for the pride of Bangladesh and I believe we can still make our country proud with this textile. All it needs is a little bit of push," disclosed the tradesman.
On our rendezvous, we also learnt that khadi was not a dying industry at all; in fact, it was a very profitable and sustainable venture. The khadi is manufactured primarily with low-count cotton, which is produced at a mass rate within the country. With help of expert designers, there is a massive possibility to turn the basic khadi into something very unique and exclusive. But like every other industry it required a minimal push, dedication from the users end, and appreciation of the artisans who were involved with the craft. If only all these three aspects worked together in sync, then we could see the khadi revive and bounce back to its previous state of glory.
Gamcha narratives
We have all seen our dads and granddads use the gamcha to dry-off after a shower, or the typical deshi farmer use the gamcha to soak away all the perspiration and tiredness after a day's labour at the field. There is not many Bangladeshi who has not heard of the term or has not seen the item, which is almost synonymous to the nation's identity.
A typical muktijoddha is pictured wearing the traditional lungi, genji with the gamcha, tied strongly at the midriff. A separate industry has developed based on the popular cloth. Even Bibi Russell, the veteran model and designer, made the gamcha print quite popular all over the world.
So, we decided to speak to one trader from the root level, to learn about the standing of the gamcha trade in Bangladesh. For that we went to Shahzadpur, Sirajganj and spoke to Al Hajj Azmal Kabir, the owner of Messrs Sunnin and Weaving Factory, which majorly deals with gamcha production and wholesale, alongside other items such as cotton saris and dupatta production.
"Our trade with the gamcha is unique. It is doing extremely well and has certainly helped us balance out the turmoil during the pandemic," revealed Azmal, to this correspondent.
On a happier note he informed us that the industry was growing in leaps and bounds, directly proportional to the increase in population. When inquired whether change in the demands of styling and fashion had any abrupt effect on the trade. Azmal replied in the negative.
"Not at all! Sales in Dhaka may have decreased by a certain percentage but it has been overtaken by increase in sales in Barishal, Jhalakathi, etc. Plus, the demand abroad has increased ten folds over the years with most demand coming from the Middle East and also Europe. In countries like the US, Australia and continental Europe, the gamcha may actually be used as a fashion item.
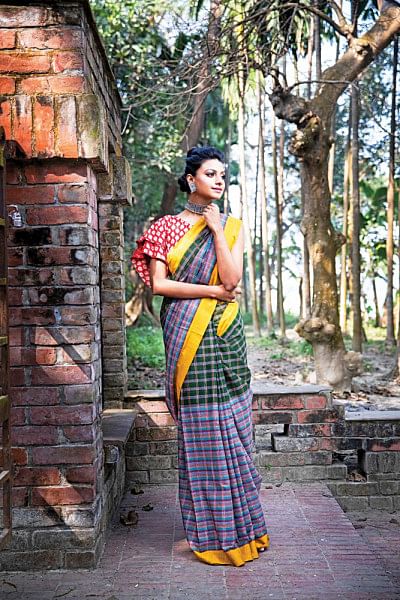
"And in the urban areas within the nation, including the capitals, town and cities, the gamcha is sometimes modified into a special towel with the same name. However, the diversifications may come about, there is simply no end to the demand and that is what is positive about the gamcha industry," Azmol revealed.
While speaking about the vendors buying the fabric from the trader, Azmol agreed that the new generation Dhakaiites preferred to have the gamcha in a new avatar.
"I have even produced saris, panjabis and kurta influenced by the gamcha print, which have been quite popular in the capital and every year during Baishakh, as these styles are worn by the young people of the nation," said the gamcha tradesman.
What we understood from the brief rendezvous was that the gamcha, a highly affordable fabric, with multitude of uses, had a promising future and could help bring in prosperity to the producers, the marketers and the retailers of the trade.
Our two cents from the research: gamcha is purely made with local thread and local weaving process and hence is a sustainable business with an ever-increasing demand.
If all the other fabric variants of Bangladesh could be dealt in the same manner, with local production, encouragement of craftsmanship and with the intense dedication to wear local fabrics, then perhaps the fabric industry in general could have thrived similar to the gamcha.
The future looks bright
Right at the beginning we spoke about the connections we are trying to establish with the fabrics of our past. Once upon a time Bengal was famous for the unique Muslin and Jamdani. We might not have reached that particular stage as of yet, but we are close and that too not with only two famed fabrics but with many others, that are also unique to our nation.
We want to inform that a Jamdani artisan currently earns around Tk 25000 to 30000 per month based on reports from the mahajan's in the Sonargaon, Narayanganj region. This is an extremely lucrative income for a craftsman, given his level of dedication behind every unique piece he produces. This also means that, a new generation of artisans will be inclined towards the unique craft and the artistry will survive. This also means that we, the users have learnt the value of handloom. That we have learnt handlooms are authentic and unique products that deserve special respect.
It's the same with every other fabric and its artisans. Bright future awaits all, we just need everyone including the world to know of our crafts and uniqueness and value them ourselves with due patronisation.
The government is also helping the fabric industry revive with the introduction of regional crafts sector like the Nakshipalli in Jamalpur and the proposed 428 crore project to boost female entrepreneurship all over the country. With continuous funding and projects like these in each and every sector, maybe it is not too far that each and every industry will revive its former glory.
Special thanks to Shaibal Saha, General Secretary, Fashion Designer's Council Bangladesh for arranging interview opportunities with root level artisans and trades people, in order to get an authentic story regarding heritage fabrics of Bangladesh.
Photo: Sazzad Ibne Sayed
Model: Arpita
Wardrobe: Khadi sari from Aranya
Model: Simmi
Wardrobe: Gamcha sari from Bibi Productions
Blouse: Zabin Iqbal
Make-up: Md. Hossen
Hair: Gazi
Styling: Zabin Iqbal
Location: Bengal Carpet Mill, Ford Nagar, Dhamrai
Comments