Revolutionising construction for a greener future
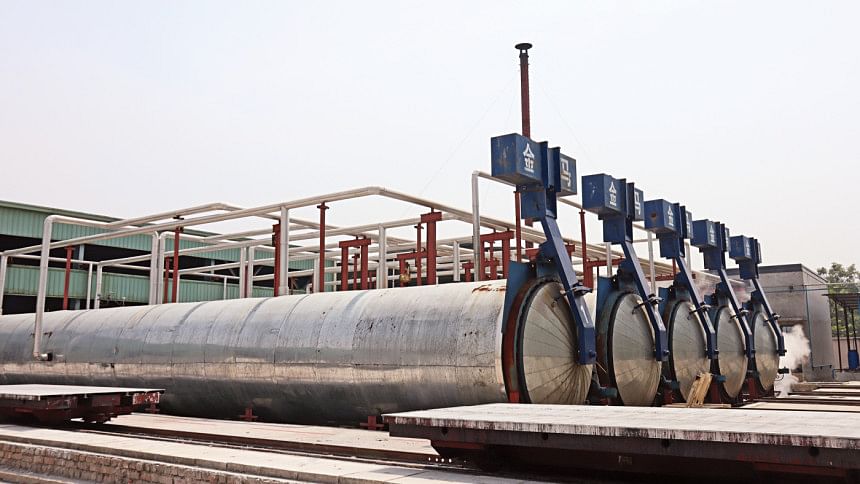
The traditional production of clay-burned red bricks is a significant contributor to greenhouse gas (GHG) emissions in Bangladesh, leading to the annual loss of 1% of the country's agricultural land. Brick manufacturing accounts for 17% of this depletion, with severe environmental consequences such as land degradation, deforestation, and worsening air pollution. Dhaka, the nation's megacity, faces a growing air quality crisis, frequently ranking among the world's most polluted cities. The city often tops the Air Quality Index (AQI), regularly exceeding 200 and sometimes reaching hazardous levels above 300, especially over the past year.
In response to these alarming conditions, the government and the construction industry are increasingly adopting innovative, sustainable solutions. One such material is Autoclaved Aerated Concrete (AAC) blocks, a next-generation construction material ideal for green buildings. These eco-friendly alternatives to traditional clay-based bricks help mitigate environmental damage while promoting responsible building practices.
In 2020, the government introduced a policy aimed at substituting traditional bricks with eco-friendly blocks in all public projects. The initiative targeted a 10 percent adoption rate in fiscal year 2019-2020, with a gradual transition to eliminate clay bricks by FY25. The Bangladesh Housing and Building Research Institute (HBRI) highlights that replacing traditional bricks with alternative materials can significantly conserve topsoil—essential for preserving soil fertility. HBRI has developed several alternatives, including compressed stabilised earth blocks (CSEBs), interlocking CSEBs, hollow concrete blocks, thermal blocks, aerated concrete, and ferrocement sandwich panels.
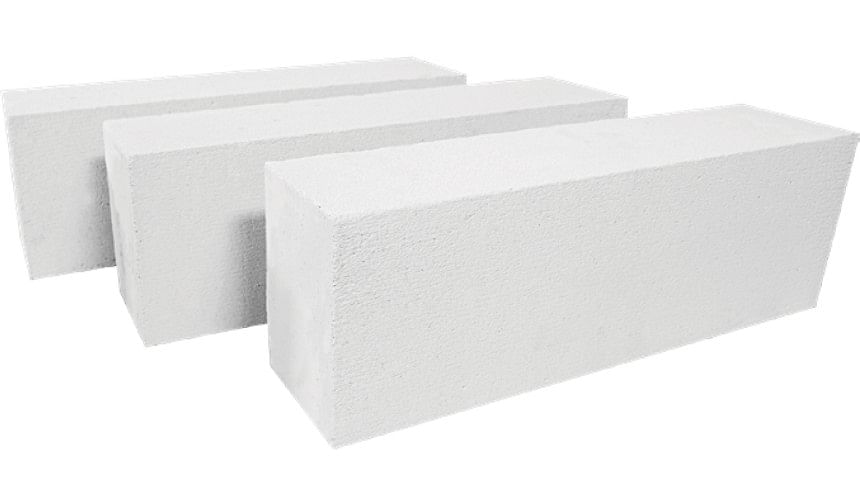
Advantages of AAC blocks
AAC blocks are unlike traditional clay-fired and hollow bricks. Their thermal insulation properties contribute to energy savings, potentially reducing energy consumption by up to 30% annually, according to a report by BUET. The lightweight nature of AAC blocks also requires less foundation, leading to savings in construction costs. "AAC block's precise sizing requires less joint mortar," says Iqbal Mahmud, Brand Manager at Nextblock AAC.
Currently, around 6,500 to 10,000 brick kilns operate in Bangladesh, producing about 22.71 billion bricks each year, according to Department of Environment data. Unlike clay bricks, AAC block production uses sand as its key ingredient, and no cultivable land is harmed in the process. "River sand, extracted from riverbeds, helps preserve aquatic ecosystems by increasing river depth and clearing unwanted deposits," adds Engr. Abu Mohammad Samsuddin of Maxcrete.
AAC blocks, made from cement, limestone, gypsum, sand, and aluminum powder, provide a fast, efficient, and superior solution for wall construction. Beyond their environmental benefits, AAC blocks offer versatility, excellent thermal insulation, lightweight properties, and fire resistance.
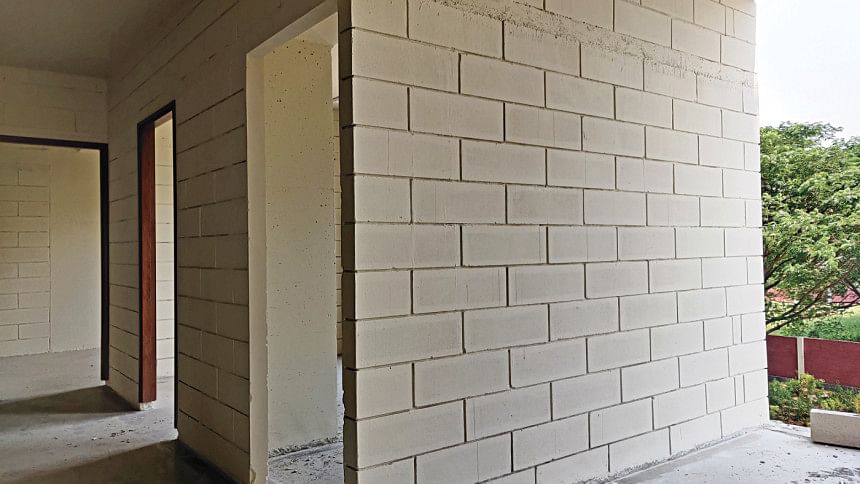
Growing presence of AAC in Bangladesh
Two companies are currently leading the charge in producing eco-friendly AAC blocks, Nextblock and Maxcrete. Nextblock, introduced by Eco Friendly Green Bricks Ltd., a sister concern of Tilottoma Bangla Group, was the first to bring AAC blocks to Bangladesh. Located in Tangail, the company utilises advanced technology to ensure high-quality, sustainable building materials, producing 500 cubic metres of AAC blocks daily.
Maxcrete, a brand of the Max Group, has invested BDT 160 crore in the green brick market. The fully automated factory in Meghshimul, Manikganj, produces 1,000 cubic meters of AAC blocks daily. This investment is part of the group's larger commitment to sustainable construction materials.
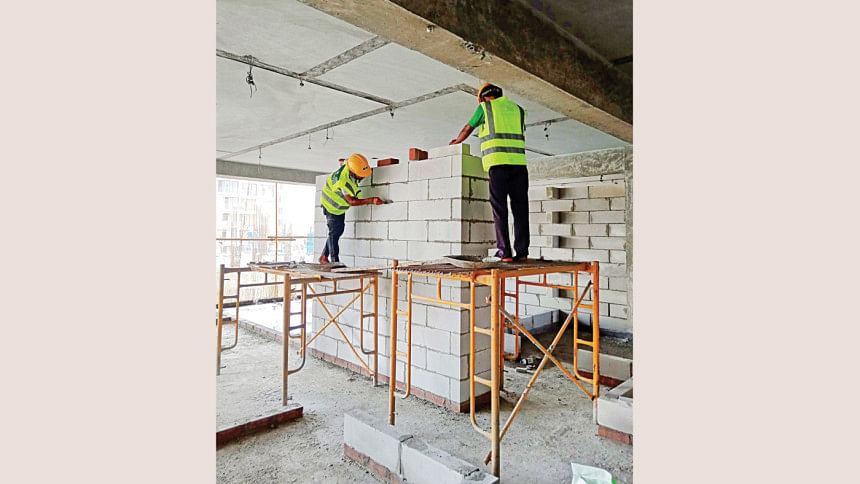
AAC blocks in construction
Beyond its environmental benefits, using AAC blocks is also cost-effective due to their lightweight properties, precise sizing, and reduced need for joint mortar. "A 110mm AAC block is priced at BDT 102, including delivery to the construction site. Since one AAC block is equivalent to seven clay bricks, and a single clay brick costs BDT 14, the total cost for seven clay bricks amounts to BDT 98—including delivery," said Iqbal Mahmud of Nextblock AAC.
Panels and blocks made of AAC are produced to the exact sizes needed before leaving the factory. There is less need for on-site trimming. Since the blocks and panels fit so well together, there is less use of finishing materials.
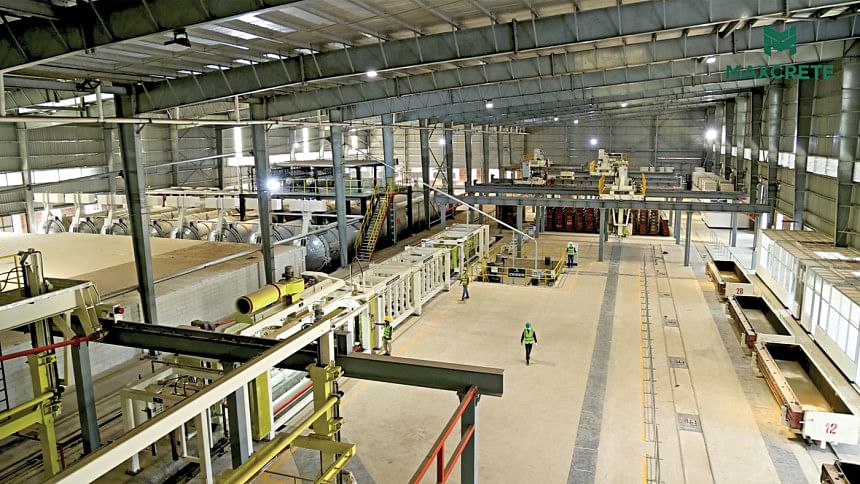
Echoing Iqbal, Engr. Abu Mohammad Samsuddin added, "When structural engineers estimate the load of a building using AAC blocks, the reduced weight significantly lowers the overall structural load compared to traditional clay bricks. AAC blocks also offer a faster construction timeline. We have observed that projects using AAC blocks are completed approximately two months faster, which has a direct impact on reducing overall construction costs by up to 20 percent, while doubling work speed due to easy installation."
Private companies, particularly real estate developers, have been actively incorporating AAC blocks into their construction projects. Additionally, these blocks are being used in selected government initiatives. However, to fully implement the plan of phasing out clay bricks in government projects by FY25, further interventions are needed to address existing gaps and ensure a smooth transition.
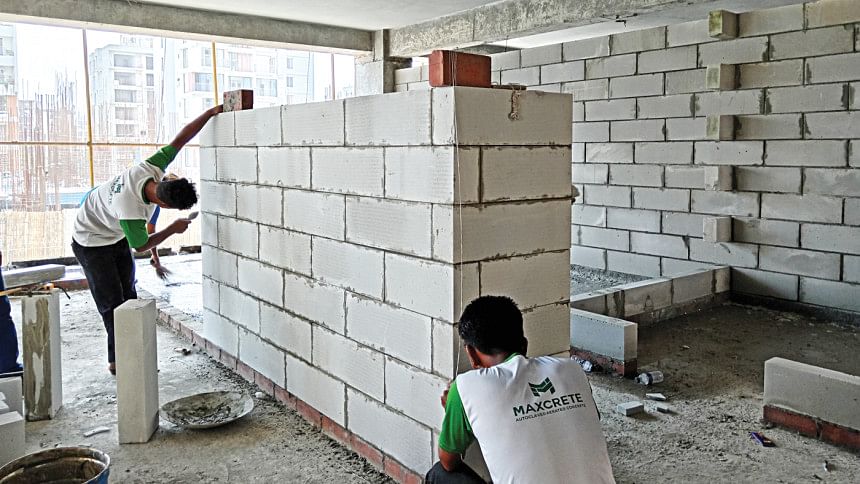
Adoption by developers
Several real estate developers in Bangladesh are incorporating AAC blocks into their projects, signaling a shift towards sustainable construction. Notable companies such as Rangs, Edison, and Rupayan are using AAC blocks in their construction. Developers in Chattogram, including Sanmar Properties Ltd and CPDL, as well as Al Aksha Properties in Rajshahi, have also embraced the material. "Rancon has banned the use of wood-fired, coal-fired, and topsoil-based bricks, opting instead for AAC blocks aligning with the company's sustainability commitment. Environmentally conscious buyers and businesses now favour projects that reduce carbon footprints and operational costs over time," says Tanvir Shahriar Rimon, CEO (Real Estate & Sea Fishing), Rancon. Many individuals are also incorporating these sustainable approaches in a multidimensional way, such as Boundry Wall Anwara Group in Bashundhara R/A which is a Personal Project.
Despite the growing interest and environmental impact, the use of AAC blocks is still in its early stages in Bangladesh. Manufacturers are providing free technical support to help construction companies manage and install the blocks effectively. As knowledge of AAC technology spreads, two more companies are emerging this year, with more expected to join in the coming years. An association of AAC block manufacturers is being formed to foster sector growth and positive environmental impact. With more developers and manufacturers adopting this technology, AAC blocks are poised to play a pivotal role in Bangladesh's sustainable construction sector. However, continued government support and patronage are essential for this emerging industry's further growth and development.
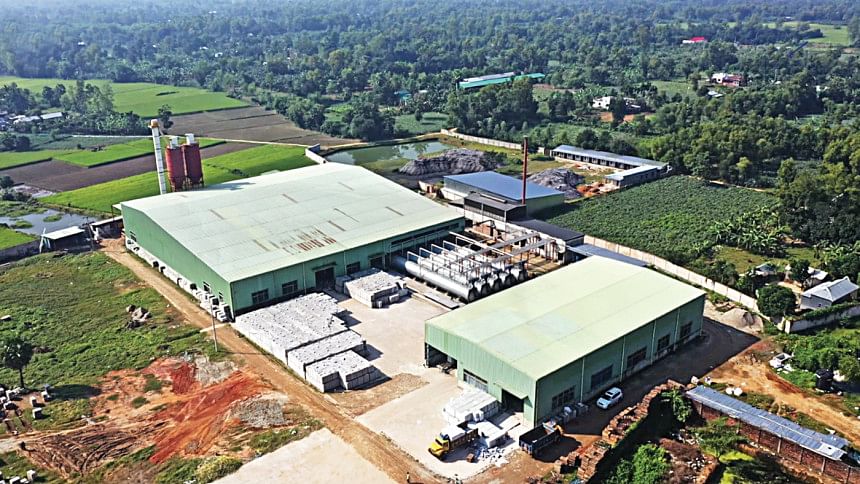
Know the ABC of ACC
- It produces 90% less pollution than traditional red brick production.
- AAC is made from quartz sand, calcined gypsum, lime, cement, water, and aluminum powder.
- AAC's lightweight, pre-cast foam material is ideal for moulding into various forms, including blocks, wall panels, floor and roof panels, cladding (facade) panels, and lintels for masonry construction.
- Due to its thermal efficiency, buildings remain at least up to 5°C 5cooler in summer.
- It is fire resistant for about 4.5 hours at a 1,250° Celsius.
- The climate resilient AAC's airiness allows water diffusion, reducing indoor humidity by absorbing moisture and releasing it outside, preventing condensation and mildew issues.
- During planning, construction costs can drop 20-25% as each block replaces seven bricks, is lightweight (7.5-9.5 kg), and requires 25% less foundation.
- It reduces joint mortar while doubling construction speed due to its larger size.
- AAC block walls require minimal water curing, as only the mortar joints need hydration, significantly reducing water consumption compared to regular bricks.
Comments