SILKEN DREAMS ONCE MORE
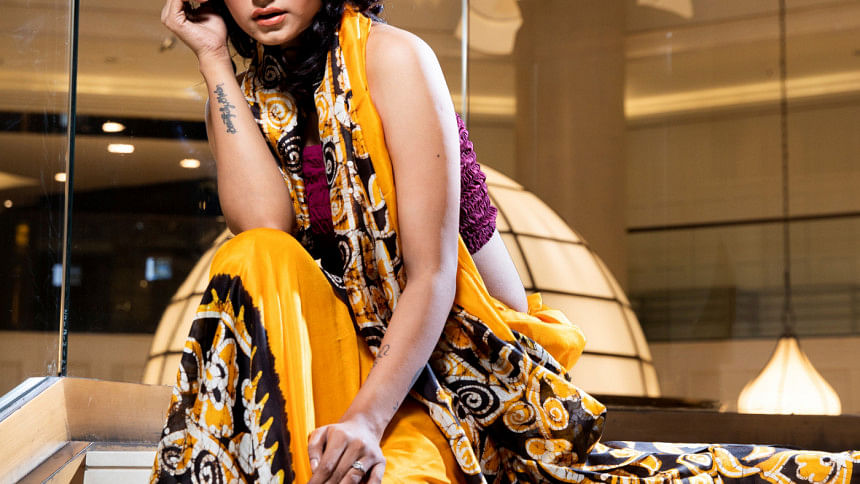
Smooth as silk is not just a saying, especially when you hold a Rajshahi silk sari against your skin. Yet, if we do not put forward our resources and policy support to the struggling industry in Bangladesh, this famed local fabric might go the same way as the Muslin, long lost in the pages of history.
At the moment, having faced repeated setbacks, Bangladesh remains firmly among the top 10 silk yarn producers in the world, despite having lost a few notches over the past two decades or so. Granted, in terms of quantity of production, output of local yarn is paltry at the moment, especially when compared to global leaders like China, India and Uzbekistan. However, the real concern lies not just with the fall in local yarn production, rather what it entailed for various small producers of silk cloth, and of course, our traditional handloom silk weavers.
Along with Bengal's famed cotton, even as far back as the 13th and 14th century, the silk produced in the northwestern regions of Bengal was coveted by those desirous of finery and luxury, and referred to as the Ganges silk.
It is no wonder either, as the variety produced here, with mulberry-fed cocoons, was and remains, among the finest. Yet, in more recent times, especially the past two decades or so, the local silk industry has faced unfavourable winds, and declined, under pressure from stronger producers in China entering the local market largely unimpeded.
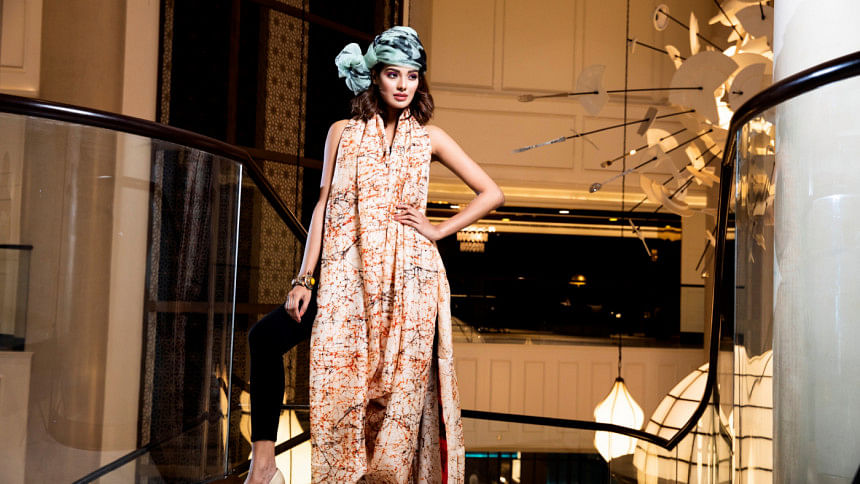
At the moment, in broad terms, the silk industry produces two types of cloth— on the power loom, and the artisan's old fashioned traditional handloom. Even as production on the power looms is largely stable per se, some of the larger mills have adapted to the yarn shortage by diversifying products and importing yarn alternatives.
The story of handlooms however, is a bit different. Many of the traditional producers of silk have bowed out of the business. A desolate gloom hangs over the many empty buildings inside the BSCIC, victims of gradual decline, reportedly, a result of faulty government policy of allowing cheaper Chinese competition to infiltrate the market in the recent past.
Yet, there are still a few resilient souls hanging on to the weaving traditions of their ancestors, like those families in Harinagar Tatipara, Kansat, Bishwanathpur, and Laharpur. Often, the entire process of creating this luxurious process is completed in-house, with various members of the family doing various jobs. Chandicharan Das, an award winning weaver and resident of Harinagar, says that supplying to Brac's silk initiative has helped the weavers hold on to this age-old tradition in his locality, allowing for decent incomes, yet it does not mean easy affluence or large profit margins, rather only fair prices and assured sales. The entire area now works on the same principle, and production is almost entirely based on dedicated orders rather than open market conditions. Some of the other younger weavers in the same area expressed interest in diversifying productions, and venture out into the world with support in the form of capital and policy.
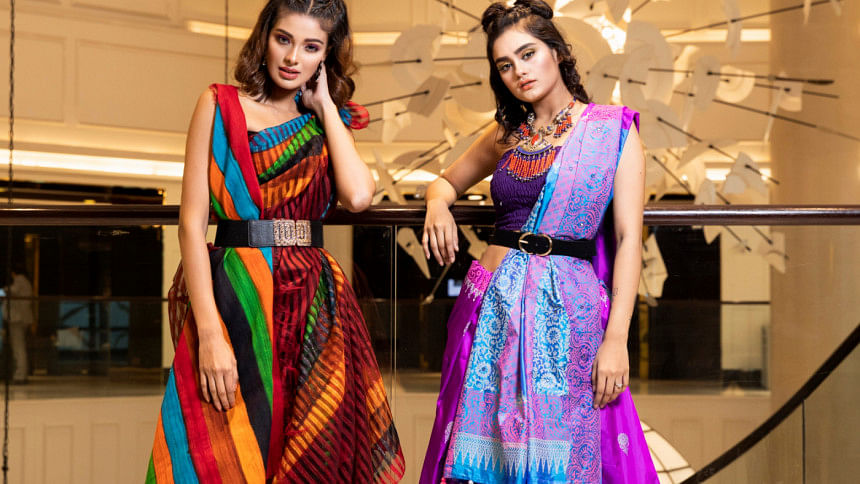
Stepping into the Tatipara, the repeated clacking of the handlooms is a rather hope inducing sound. In that area alone, there are still some 800 active handlooms. The main problem faced by the weavers, as most artisans, is the lack of financial growth, and the lure of other easier professions to make money. At the moment, the hourly wages of a handloom artisan ranges between Tk 60-65 per yard, and given the labour intensive nature of weaving, and its slow pace, daily incomes rarely exceed Tk 200, forcing many of the younger members of the weaver households to opt out of the profession. The work is also skill intensive, requiring apprentices to invest long months and years into learning it. Combined with the prices of yarn, and other expenses, it is very difficult for small and even medium handloom weaving operations to make and sustain decent profit margins, Dukkhuranjan Das, a local weaver, explained. Here too, much of the work is kept in-house, with women of the household degumming the cloth and making reels of the yarn to use on the loom, tirelessly working on the traditional charka. Industry insiders estimate the total number of active silk handlooms is no more than 2000, which is a significant fall.
Despite the setbacks, weavers in Rajshahi are still crafting beautiful yards of silk cloth, in varieties like Balaka, endi and raw silk.
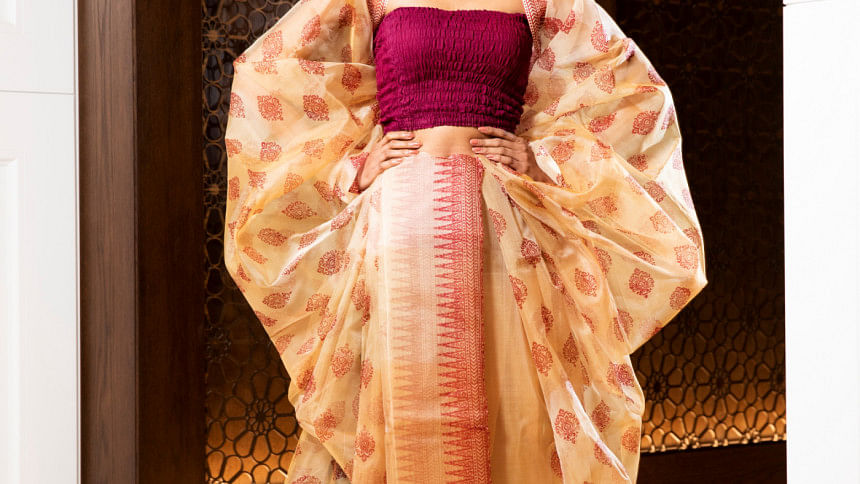
For the small supplies of local yarn still maintained, we can still claim with pride the continuation of the famed Bengal silk. But even today, the authenticity of that claim can be questioned by discerning consumers, if we look into the origins of the yarn, and the mode of weaving. To preserve the true tradition of Rajshahi silk, we must take action soon, with proper policy support, investment grants, and training programmes to retain the heritage of pure local silk, spun and woven by hand, and ensure substantial remuneration for all weavers and artisans, even if just to preserve this pride of Rajshahi.
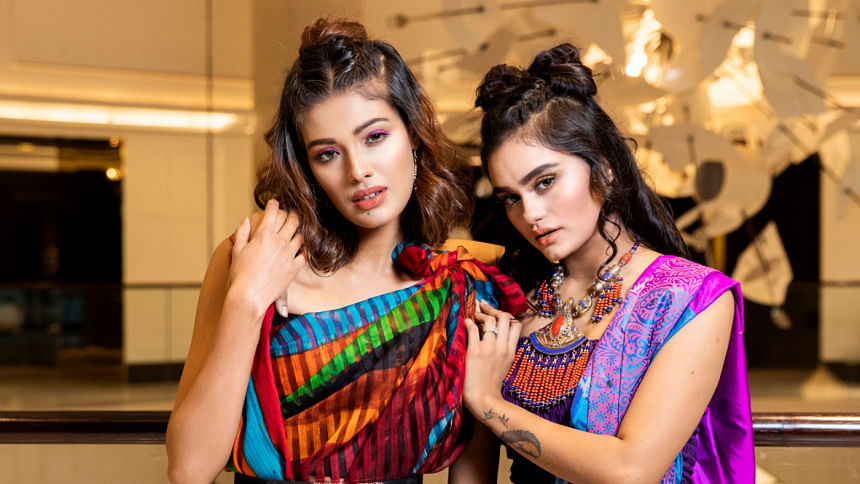
Photo: Sazzad Ibne Sayed
Styling: Sonia Yeasmin Isha
Model: Arpita, Riba
Wardrobe: Doyel Silk
Jewellery: Kolors of Kathmandu
Makeup: Farzana Shakil's Makeover Salon
Location: InterContinental Dhaka
Comments