Employment in the age of automation
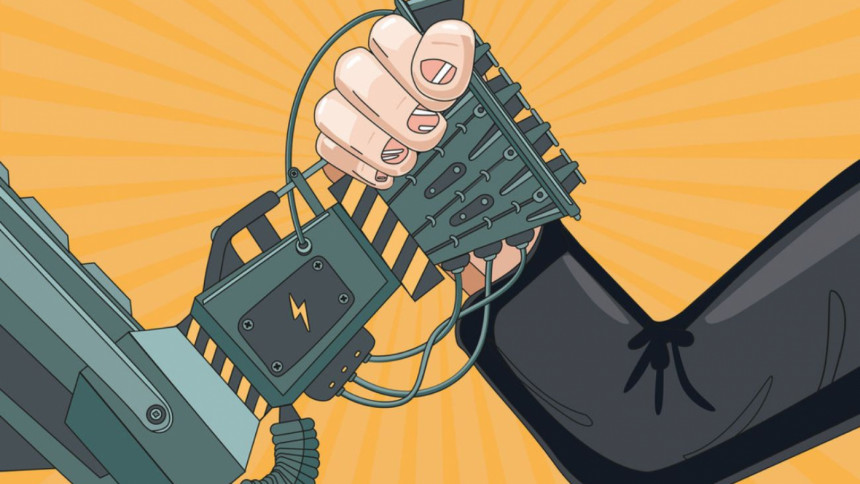
The lift-operator is a peculiar person. He sits on a stool inside a small, claustrophobic space. In the olden days his job required quite a few skills. Back then, lifts were manually operated with a large lever, and it was the responsibility of the lift-operator to regulate the speed of the lift. His task also involved synchronising his timing in order to make sure that the lift always stopped parallel to the floor. It was almost as exciting as landing an aeroplane. However, nowadays most lifts can be operated by the user with the mere push of a button. Today the lift-operator is understandably miserable in demeanour. His once engaging occupation has been transformed into a humdrum reality. Only a handful of lift-operators will be able to work at the Eiffel Tower in Paris or the CN Tower in Toronto. He knows that his days are numbered.
The lift-operator is not alone. The fourth industrial revolution set off a wave of technical progress that has since been going forward at a remarkable pace. With the advent of modern technology, automation of production processes has led to loss of jobs for workers, even in industries where it was previously thought to be impossible. As it becomes increasingly obvious that automation is unavoidable and unrelenting, should human beings prepare to become obsolete?
Nowadays machines are taking over work from humans in every field. Industrial robots are becoming more common than before in almost every country. Today there are cars, buses, and trains capable of driving themselves. Supercomputers are now able to defeat grandmasters in a game of chess. Thanks to facial recognition technology, computers can now recognise humans better than humans can recognise computers. Even creative tasks like painting and music could soon be done with computers, once they are pre-programmed with the algorithms for picturesque scenes and pleasant tunes.
According to a recent article published in The Economist magazine, China's installations of industrial robots rose by 59 percent in 2017. In some Chinese ready-made garment (RMG) factories, workers are being outnumbered by machines. Cameras, originally made for the military, are being used to scan for flaws in fabrics by utilising artificial intelligence. Chinese RMG factories are witnessing not only a precipitous fall in employment, but also a profound shift in the nature of jobs. Workers who were previously occupied with monotonous tasks are now assisting engineers in designing better machines for the assembly line.
Automation has already started to affect Bangladesh's labour market. Robots have been introduced in some RMG factories. According to estimates by Access to Information in Bangladesh (a2i), 60 percent of jobs in the RMG sector in Bangladesh may disappear by 2040 due to automation. The extent of automation can only be expected to increase in the future. Due to pressure from labour rights groups, environmental groups, and international compliance laws, it will be difficult to sustain the large number of RMG production units that currently exist in the country. The most likely outcome is that the number of RMG production units will decrease in the future. Most of the small RMG factories will be either forced to shut down or be taken over by larger companies. As a result, the market share will become more concentrated.
As most of the surviving RMG firms will all be quite large in size, they will invest a substantial amount of resources in automation, in order to boost their productivity and profits. Technology adoption is directly related to factory size. According to a study by the Centre for Policy Dialogue (CPD), use of advanced technologies in the RMG sector of Bangladesh is prevalent in 47 percent of large-scale RMG enterprises, compared to 25 percent of medium-scale RMG enterprises.
Automation has the potential to destroy jobs for workers, especially jobs that involve simple repetitive tasks. Thus workers who are at the very bottom of the production process, and who are often female, are highly vulnerable to loss of jobs due to automation. On the other hand, automation will also create new jobs. Machines will require operators and repair technicians. Some workers who have the necessary education and training, and who will probably be male, will take up these jobs. Automation will create winners and losers, and widen the gulf between male and female employment. Thus automation poses a serious threat not only to employment, but also to gender equality.
Countries should specialise in the production and export of goods that intensively use their relatively abundant factor of production. In other words, capital abundant countries should specialise in the production and export of capital-intensive goods, whilst labour abundant countries should specialise in the production and export of labour-intensive goods. Bangladesh, being a labour abundant country, specialises in the production and export of RMG, which is hitherto a labour-intensive industry. If the RMG industry becomes more capital intensive as a consequence of automation, Bangladesh will have to look for a new sector for specialisation that will be sufficiently labour-intensive to absorb its enormous young labour force. The rise of automation means that the hour of reckoning has arrived for policymakers to redesign the existing anachronistic education system, whilst at the same time, revisit efforts to create the jobs of the future.
Syed Yusuf Saadat is a research associate at the Centre for Policy Dialogue (CPD).
Comments