Beyond the Accord
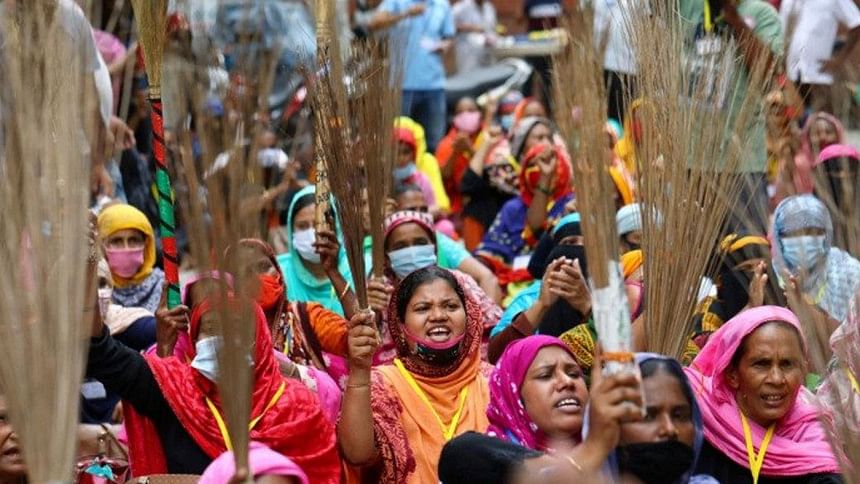
Eight years ago, one of the worst industrial disasters in history—the collapse of an eight storey commercial building in a sub-district of Dhaka—demonstrated to the world the heavy price of producing cheap clothing to fuel the "fast fashion" industry for consumers in the global North. After the Rana Plaza disaster in 2013, the international response concentrated on technocratic approaches to address the lack of worker safety measures by focusing on fire, electrical, and structural improvements to a portion of the country's registered factories. The Accord's tagline is: The Accord helps ready-made garment (RMG) factories in Bangladesh become safe—and stay safe—for millions of workers.According to the Accord's website, 93 percent of factories have completed the initial remediation process on safety issues that were identified during inspections. After spending USD 11 million per year on supporting engineers and monitoring staff, we must ask ourselves eight years later, are garment workers in Bangladesh safer now than they were before?
Complex global supply chains, of which Bangladesh and other garment exporting countries are an integral part, are characterised by hyper-flexibility, a lack of transparency, and unequal power dynamics, all of which are seen as essential features for these complex networks to function. These characteristics are not necessarily likely to promote—and in fact frequently undermine—respect for good labour rights. For decades, many global brands and buyers have been able to use their unequal distribution of bargaining power within these supply chains to require their suppliers to meet the competitive pressures within the industry by producing smaller batches of increasing varieties of products more rapidly and at decreasing prices.
Researchers (Kabeer, N; Haq, L; Sulaiman, M, 2019) have found that since 2013, there have been improvements in certain workers' outcome standards (mainly better health and safety conditions, relative job security and improved social benefits) and process rights (primarily representation in worker participation committees). This is significant because it is critical that workers feel that their physical place of work is safer than before, not likely to collapse or catch on fire; and if there are any signs to the contrary, they are being trained how best to handle it.
Despite these gains, however, due to the power dynamics between the various actors in the industry and the difficult nature of the work itself, garment workers (female garment workers in particular) continue to face sexual harm and suffering, gendered industrial discipline practices (including physical violence, verbal abuse, coercion, and threats), severe health consequences, barriers to freedom of association and collective bargaining, low wages, long working hours, and retaliation for reporting abuses.
Unfortunately since 2013, the focus has been on a very narrow definition of what constitutes safety for the millions of garment workers in the industry. Adhering to this limited notion has been dangerous because it has lulled us into complacency and absolved global brands of real responsibility. This limited approach has served to reassure global retailers that they can continue "business as usual," now that buildings themselves are structurally sound, while continuing to pursue a sourcing strategy that contributes to overall declines in the mental and physical health of workers and leaves them insecure and without any social protections.
This lack of progress in many critical areas to improve labour rights created a situation that was ripe for suffering under an unanticipated and unprecedented global crisis. A newly released report by the Institute for Human Rights and Business (IHRB) and the Subir and Malini Chowdhury Center for Bangladesh Studies at the University of California, Berkeley (with the support of UNDP Bangladesh and the Government of Sweden), "The Weakest Link in the Global Supply Chain: How the Pandemic is Affecting Bangladesh's Garment Workers," captures the responses of global brands during Covid-19 and the subsequent effects on workers in the immediate aftermath. The report, drawn from in-depth interviews with international brands, Bangladeshi suppliers, representatives of international civil society, and Bangladeshi labour activists, seeks to understand the impacts of the pandemic on the industry and its workers, and it proposes changes to policies and practices that can lead to long-term improvements in the sector.
This global pandemic has put a glaring spotlight on the unequal power dynamics that were always present in the system. Because the larger structure of the global supply chain was intentionally left intact after 2013, many of the statistics that emerged at the onset of the pandemic, like 98 percent of buyers refused to contribute to the cost of paying the partial wages to furloughed workers or 72 percent of furloughed workers were sent home without pay were, unfortunately, not at all shocking (Anner, 2020).
During the Covid-19 pandemic, already difficult conditions were made even more precarious for the millions who depend on these jobs for their livelihoods. Many Bangladeshi factories supplying to international brands consolidated their business and some went under. Bangladeshi workers suffered a 35 percent pay cut during the month of lockdown. Millions of garment workers found themselves out of work, furloughed without pay, and their savings depleted (for example, the report finds that 65 percent of female workers said they didn't save or used their savings to buy food)—all of this occurred without a safety net to fall back on. Not surprisingly, workers have faced critical challenges to their mental health and overall emotional wellbeing during this time; 82 percent said they felt afraid that something awful might happen and 71 percent said they felt down, depressed, or hopeless. Kalpona Akter, founder of the Bangladesh Center for Workers' Solidarity, told the authors that Covid-19 only heightened what has already been in places for so many decades, "…all these years, business has only given us empty promises, nothing more than that. They're always [focused] on their profit sheet, their closing reports. When we needed them most, they just left us in a starving situation. They did not take on responsibility." Transnational labour organising groups were successful in making brands aware of the reputational risks they were exposed to and as a result of their activism, USD 20 billion dollars were paid to suppliers in Bangladesh.
To make lasting changes for workers in the industry, as the report notes, responsibility must be upheld at all the layers of the supply chain. For example, the government of Bangladesh must enforce existing laws and standards, protect workers without formal contracts, enable them to form unions, establish grievance mechanisms, and provide a safety net. Global brands need to ensure that their actions do not squeeze their suppliers. They should oversee their factories so that international standards are met, avoid cancelling contracts, and pay for raw materials already acquired and work already undertaken. Local suppliers, who bear direct responsibility for the wellbeing of their workers, should provide for the necessary infrastructure to ensure safe working conditions and adhere to the disbursement wages and other benefits as required by local laws.
This limited definition of what constitutes safety for garment workers has resulted in narrow and incomplete interventions over the decades and particularly over the last eight years, which have not only been inadequate, but have also been harmful. We have accepted limited improvements as significant and overarching progress. Now, as Bangladesh's garment workers weather the aftermath of a global pandemic, this is the ideal time to work towards a more ethical and sustainable industry—one that works to disrupt the unequal power relationships between global brands, suppliers and workers. In order to make a real difference for workers working in garment factories around the world, they must experience "safety" in the fullest sense of the word—a definition, if fully understood, would be one that would encompass protections to their health, wellbeing, and livelihoods.
Sanchita Banerjee Saxena, PhD is Director, Subir and Chowdhury Center for Bangladesh Studies, University of California at Berkeley, and Editor of Labor, Global Supply Chains, and the Garment Industry in South Asia: Bangladesh After Rana Plaza (Routeledge, 2020).
Comments