Investment dries up in dyeing sector as gas shortage lingers
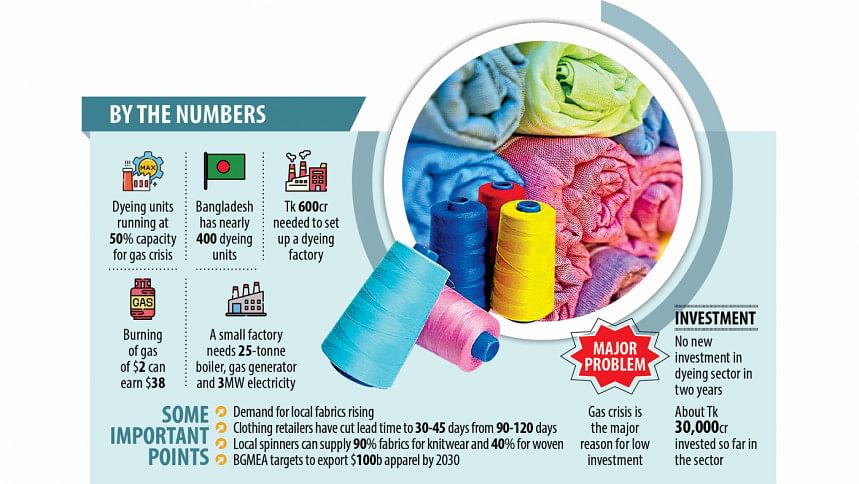
Investment has dried up in Bangladesh's dyeing sector, a vital cog in the textile and apparel supply chain, owing to the dragging gas shortage despite higher demand for fabrics from local garment exporters, industry people say.
Not a single new dyeing unit has been set up in the country in the last two years because of the energy crunch and a spike in the investment needed to establish such a facility, said Monsoor Ahmed, chief executive officer of the Bangladesh Textile Mills Association (BTMA), a platform of the primary textile sector.
Inadequate supply of gas has been an issue for textile millers for a long time since local production has not kept pace with a surge in demand for energy. This prompted the country to turn to liquified natural gas (LNG) in 2018.
But a US dollar shortage forced the government to halt buying LNG from the international spot market in the middle of last year, dealing a blow to industries as gas supply declined.
Although the government resumed buying the super-chilled energy from the international spot market at the beginning of 2023, industries have not overcome the energy shortage entirely.
Textile millers say the dearth of fresh investment lingers since existing dyeing units are already running at half their capacity although there is a glut of orders from both local knit and woven fabrics manufacturers.
In Bangladesh, the consumption of locally made fabrics is rising as international clothing retailers and brands have shortened their lead time to 30-45 days from 90-120 days to remain competitive globally.
This means garment exporters have no other way but to use local fabrics since imports from China and other countries take time and will make it difficult for manufacturers to supply finished products within the agreed deadline if they continue to rely on the external market for textile products.
Currently, local spinners can supply nearly 90 percent fabrics and weavers can meet more than 40 percent of the demand for fabrics from garment manufacturers, who accounted for more than 85 per cent of Bangladesh's export earnings of $55.50 billion in the last fiscal year.
Owing to the higher inflow of orders and the truncated lead time, many dyeing industries have already been transformed into composite units, which consist of the facilities and processes involved in turning textile raw materials into fabrics.
In Bangladesh, nearly 400 large dyeing units are capable of meeting the entire demand for knit and woven fabrics.
"We have a lot of work orders from garment manufacturers and suppliers. Even 800 dyeing units can run smoothly amid the current flow of orders," said Md Azahar Khan, chairman of Mithela Group, a textile and garment producer in Narayanganj.
He said despite the huge business opportunity, local dyers can use 50 percent of their capacity because of the gas crisis. Operating dyeing units and boilers needs a lot of gas pressure, Khan said.
Some of the dyeing units are running using rice husk, but securing such a big volume of the protective coverings of grains is a challenge for millers, he said.
Md Saleudh Zaman Khan, managing director of NZ Tex Group, also a Narayanganj-based textile and garment unit, said he used to run his boiler with coal in the past for dyeing purpose but it is not possible now because of the environmental compliance demanded by international clothing retailers and brands.
"Sometimes, diesel is used but it is expensive."
NZ Tex is currently dyeing 1.25 lakh metres of yarn daily against its capacity of two lakh metres.
Zaman underscores the importance of a smooth supply of gas, saying a $2 used to burn gas in the textile sector can generate revenues of $38.
"So, if gas is not supplied adequately in the dyeing sector, garment export may witness a decline."
Monsoor Ahmed said setting up a dyeing unit would cost Tk 200 crore to Tk 250 crore a few years ago but now it requires Tk 500 crore to Tk 600 crore.
This is because dyeing units need modern effluent treatment plants that are expensive and modern boilers, he said.
"It is really hard to come up with such a big investment plan at a time when gas supply is insufficient," said Mohammad Ali Khokon, president of the BTMA.
"Nobody wants to take the risk as the gas supply situation is not improving. Running boilers and generators with the current pressure of gas is not possible."
According to Khokon, under the current financial crunch, it is not possible to invest Tk 500 crore to set up a dyeing unit.
He warned that if adequate gas is not supplied to primary textile units, achieving the garment export target of $100 billion by 2030 might not be possible.
Comments