Don’t let labour shortage derail our RMG momentum
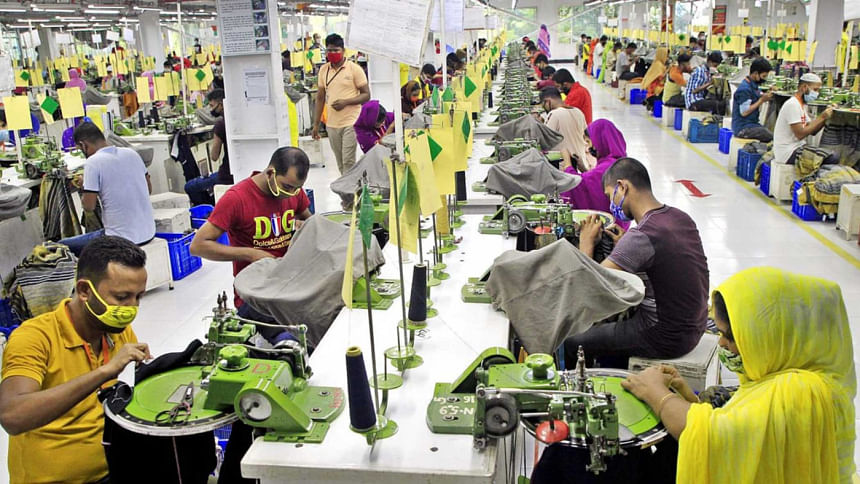
Our RMG industry has been characterised by the phrase "feast or famine" these last two years. After Covid-19 broke out in early 2020, clothing orders were extremely hard to come by for a period of time. Business picked up briefly, then slumped again, then really gathered pace towards the end of 2021. It has not stopped since.
This volatile business environment presents several challenges before us, the RMG manufacturers, and one of them is staffing. Forced to let workers go during the pandemic, RMG factories are now scrambling to hire workers to meet record orders. Unfortunately, the demand for workers is exceeding supply, and skill shortages are now a real issue in our industry. Rumours I have heard suggest that we have a worker shortage of 15-20 percent. In terms of numbers, this represents hundreds of thousands of garment workers—the lifeblood of our industry.
Why do we have this problem? There are several factors at play. The first is the unprecedented uptick in orders. Bangladesh broke records in RMG exports in the last quarter of 2021, and this momentum has been carried over to 2022. The shipping crisis in China doesn't look like it will go away until the end of this year either. So, Bangladesh has become a safe haven for RMG production, even if we ourselves are not completely immune to logistical challenges at the moment.
Amid the record number of orders, we face a crisis of labour. Many of the RMG workers who were terminated as orders were cancelled were forced to return to their village homes. There is evidence that suggests that many of them have left the garment industry for good. If this really is the case, it's a huge loss for our industry. Besides, many garment workers have gone abroad in search of work in other RMG-producing countries. I recently saw a report quoting that 40,000 Bangladeshi workers are currently employed in the Jordanian garment sector. Others have left to work in the garment industries in Mauritius and Malaysia.
We need these workers now more than ever, in what looks to be a huge year for our RMG industry. Our factories might typically run at 50-60 percent capacity, but at present, many are operating at around 90 percent. Record levels of garment exports are on the cards in 2022, but this success story could turn into a pipe dream if we don't tackle the staffing crisis in time.
How do we address this crisis? I believe there are several options.
In the short term, there are several tactics that we could adopt. We could raise wages and other fringe benefits to attract more workers to join our factories. This could include bonuses or benefits such as sign-on incentives. Another option is flexible working practices. This includes facilitating the re-entry of working mothers into the workplace through implementing alternate working hours, creche facilities, and so on. These are areas that a progressive business should be addressing anyway, so now might be a good time to invest in such human resource strategies.
In the medium-to-long term, two obvious solutions spring to mind. The first is a better, more coordinated skill strategy for our industry. There is compelling evidence that upskilling workers results in near-term efficiency gains and a reduction in defects. Are our current workers skilled enough to meet future staffing requirements in our sector? During the pandemic, Shimmy, an industrial edtech startup that upskills RMG workers, conducted the Apparel Automation Pulse study in Bangladesh. The study uncovered increased investments in advanced machines in the sector, and the skill gaps alongside it. There is no time better than now to expand this type of research and make sure that we have the right systems and processes in place.
The second step is to look at production levels as well as automation. Are factory workflows in our industry established as efficiently as they could be? Could better, more qualified management make a difference in this area? The two go hand in hand. It is also time to consider possibilities for investment in technology that could boost productivity. If orders remain high, factories will have the opportunity to boost cash reserves. This should improve the opportunities to invest in operational capacity and efficiency. Some amazing new solutions for garment factory automation are available right now. With the world's textile events and exhibitions now opening once again for face-to-face business, we as factory owners need to be looking at ways we can use them to future-proof our industry, and to help us better manage fluctuations in orders and output requirements.
Mostafiz Uddin is Managing Director of Denim Expert Limited, and Founder and CEO of Bangladesh Apparel Exchange (BAE) and Bangladesh Denim Expo.
Comments