Promoting eco-friendly production process in the RMG sector
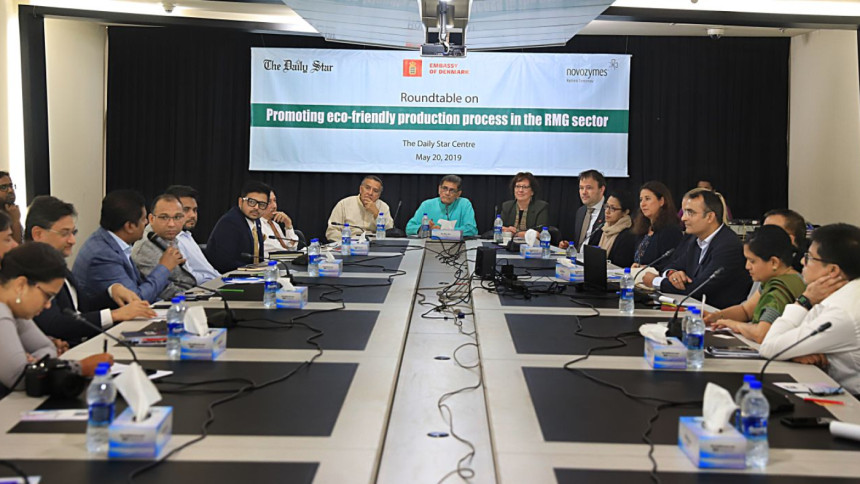
Mahfuz Anam, Editor & Publisher, The Daily Star
The key question of today’s discussion is how we can sustain the growth of the RMG sector and yet protect our natural resources. We are most concerned about water. The Daily Star has written umpteen times about pollution of water sources due to inefficient management of industrial wastes. In most cases of industrial production, water is considered to be practically free. The manufacturers never calculate the cost of water they are using to produce their products. We are living as if there is no tomorrow. We have now come to a point where we can’t afford to be reckless anymore about our environment. Today’s discussion is not against anybody; it is for Bangladesh; it is for the sustainable development of our RMG sector.
Winnie Estrup Petersen, Ambassador, The Embassy of Denmark in Bangladesh
Bangladesh has come a long way in the RMG sector. It has also progressed in terms of achieving energy efficiency. Many industries have significantly reduced their energy consumption. But we don’t see much improvement in the use of water. Water is the heart and backbone of Bangladesh. Bangladesh needs to optimise the use of this precious resource.
There are available solutions that can reduce the negative impact of garment production on the environment. One such example is the use of enzyme in the production process. It can help reduce environmental footprint by saving two-thirds of water and 50 percent of the energy in the wet processing of the garment sector. It is a non-toxic alternative to polluting chemicals. As a result, there will be overall improvement in productivity.
As retailers and customers become more conscious, the sustainable production of clothes will be a requirement, not an option. Increasingly efficient, safe and eco-friendly solutions will give Bangladeshi RMG sector much better branding and a competitive edge in the global market.
Radhey Kaushik, Regional Marketing Manager (Asia Pacific), Novozymes A/S
Novozymes A/S is based in Copenhagen, Denmark. We have been in the business of enzymes and microbes for over 70 years. We are the market leader in providing biological solutions. We serve different industries in 130 countries around the world.
Globally, the production process of the textile industry is putting heavy pressure on the environment. New opportunities are opening up in sustainable textile manufacturing. Enzymes let textile mills and laundries save energy, time and money. Consumers and brands get the high-quality, sustainable fabrics that are swiftly rising in popularity. In 2018 alone, through our different bio-solutions such as desizing, bioscouring, bleach clean-up and Combipolish, we saved water equivalent to 3 million Olympic size swimming pools, eliminated CO2 emission equivalent to removing 2.65 million cars from the road per year and reduced consumption by approximately 1.5 million tons of chemicals We are not simply stopping at providing clean water, saving energy but at the same time we are creating a better environment by removing harmful chemicals. Biological solutions also significantly increase efficiency and productivity.
The RMG sector in Bangladesh has huge potential. But it needs to grow in a way that will ensure development of the sector as well as save nature. Novozymes can make significant contribution in this regard.
The production process using biological enzymatic solutions could be further strengthened through developing local formulation rather than relying on imports of finished enzyme products. The initiation of local formulation industry seems less attractive due to high tax on import of enzyme raw materials. Lowering of tax on enzymes can create space for innovative solutions which can drive the necessary customisation for the Bangladesh RMG industry.
Louise Lihn, Global Market Communications Partner, Novozymes A/S
As we use more clothes than ever before, we also generate more textile waste which is harmful to the environment. Hence, we need to change our habit and promote long-term use of clothes. Biological solutions can help prolong the lifetime of clothes significantly by improving the quality, strength and appearance.
Furthermore, we see that consumers’ habits are changing. They are looking for sustainable indicators in the market. To produce a normal pair of jeans and cotton t-shirt, it requires more than 10,000 liters of water. Consumers are becoming more and more aware of how fashion has a negative impact on the environment. That’s why when they buy clothes, they want to know the footprint of the product and the quality of the clothes. We are trying to educate brands and consumers about these issues so that they can make an educated choice about the garments the brands are selling, and the clothes consumers are buying. Consumers should try to avoid poorly produced clothes and we need to help them in making the right choice and the sustainable choice by creating transparency in the market.
Rafee Mahmood, Director, Mahmud Group
In our factory, we have been able to significantly reduce the usage of water in washing jeans. We have sourced responsible technologies and chemicals that help break down enzymes into nano-bubbles. Earlier, it used to take 300 litres of water to wash a pair of jeans; now we can do it using only a cup of water.
Mohammed Zahidullah, Head of Sustainability, DBL Group
There are huge opportunities for saving water in knit manufacturing. Lesser consumption of water also helps conserve energy and reduce usage of dyes and chemicals. Earlier, it used to take 120 litres of water to dye 1kg of fabric. We have reduced it to 60 litres through incorporation of eco-friendly production processes in our factory.
The challenge for manufacturers is that on the one hand, the cost of doing business is going up and on the other, buyers are paying less for the products. Hence, it becomes difficult for the manufacturers to invest in eco-friendly technologies.
Nishat Chowdhury, Programme Manager, PaCT (Partnership for Cleaner Textile), IFC
The PaCT programme was launched in 2013. It has recommendations on cleaner production processes. The 200 industries that participated in the programme have implemented various green production measures. These factories have been able to save 22 billion litres of water per year and reduce chemical consumption by 460,000 tonnes. Besides advocating for eco-friendly production process, the programme has also addressed the challenge of access to finance for adopting new technologies. We have been able to establish a USD 200 million export development fund for the sector. We have also been able to mobilise the National Board of Revenue (NBR) to increase custom duty on some toxic chemicals.
We need to make our brands and designers aware so that when they design recipes for a garment product, they avoid use of harmful chemicals. We also need to promulgate industry-specific regulations for consumption of water, chemicals and energy.
Jacob Kahl Jepsen, Head of the Danish Trade Council, Embassy of Denmark in Bangladesh
90 percent of the manufacturers are catering to the export market. A lot of efforts and investments have been made to bring more sustainability into the sector and in production. The new factories are using state-of-the-art technology but the majority of the factories was built some years back and is less efficient. We need to support these factories to become more sustainable. Another segment is to look at the remaining 10 percent catering to the local market.
We need to seriously look into the compliance issues of the garments manufacturers who cater to the local market.
Bangladesh needs to diversify the whole production process of RMG products. The country should explore ways to be less dependent on import of raw materials and technological solutions. There is a huge opportunity to develop local formulation which will create employment for more people as well as make the industry more productive by shortening lead time.
Bangladesh should set KPIs for reducing the environmental impacts of the RMG production process. Bangladesh is lacking an overall strategic plan for the RMG industry. We only understand the effort to have a 50 billion USD export potential established – but what about having a KPI for environmental considerations?
Monower Hossain, Senior Director, BGMEA
Most pollution occurs in the wet processing part of the RMG production process. Among BGMEA members, not more than 250 factories do wet processing. Most of our factories are sewing-based.
Currently, Bangladesh has 85 LEED-certified factories of which 23 are platinum rated. Of these 23, six factories are among the 10 best factories in the world. This has been achieved by the factories themselves, not by any national regulation or by any international pressure. Apart from their own business case, factories don’t get any incentive for investing in green production process. Both green and non-green factories get a price. Hence, the sourcing model needs to be revisited.
Md. Moshiul Azam Shajal, Vice President, BGMEA
Almost all the export-oriented factories in Bangladesh are fully compliant. The problem lies with the industries that cater to the local market. These factories are seriously polluting the environment as most of them are not compliant. We need to seriously look into this issue and take immediate action to bring those industries under regulation.
Ethel Laursen, Business Unit Director, EMA-AP, Novozymes A/S
Enzyme solutions could be perceived as more expensive than chemicals when comparing kilo prices. But usage of enzyme significantly reduces consumption of resources such as water and energy. If we look at the total cost of production including cost of water and energy, enzyme usage is much cheaper than chemicals. We are trying to share this knowledge with Bangladeshi manufacturers.
There are some regulations in Bangladesh that are making the import of enzymes difficult. In the last year, lesser amount of enzymes entered Bangladesh because some kind of threshold had been put on enzymes. We are advocating for incentivisation of enzymes because enzymes are going to support the textile industries to be greener and to be more sustainable. There should be a different kind of import tax for enzymes compared to harmful chemicals.
Azmal Hossain, Managing Director, Brenntag BD Ltd
In Bangladesh export-oriented factories are allowed duty-free import of raw materials. The government should extend same facilities to producers of enzyme formulations. Only then will it be possible to provide enzyme solutions at a cheaper rate.
Tareq Rahman, President, Nordic Chamber of Commerce and Industry in Bangladesh
Small initiatives like using energy-efficient lights and pumps can make a big difference.
Access to finance for implementation of green initiatives still remains a challenge. There should be a green fund to support eco-friendly production process in the RMG sector.
Metering system should be introduced to track usage of water in factories. The government should also formulate legislation regarding efficient use of water.
Mohammad Shahidul Islam, DGM-HR, Admin & CSR, Epyllion Group
Epyllion has earned many national and international certifications. Unfortunately, they are not adding much value to our products in terms of getting better prices. BGMEA should help us take the issue to international platforms and motivate buyers to pay for green initiatives.
We have been using flowmeter for the last 10 years to measure the usage of water in our factories. We have also been able to reduce water consumption by 30 percent.
M Jahangir Alam, Head of Operation, Genesis Fashions Ltd
We need suitable substitutes for harmful chemicals. There are some solutions available in the market but they are expensive. I would request Novozymes to look into this issue and develop affordable products for Bangladeshi manufacturers. The buyers should also share the cost of these additions.
Mahbubur Rahman Khan, Assistant Director, Department of Environment (DoE)
Although there are no specific regulations for ensuring efficient use of resources in Bangladesh, we can still take pro-active action to show our concerns for environmental protection. Regarding the issue of access to finance, I would like to request local manufacturers to utilise the benefit of Joint Crediting Mechanism.
Comments