RMG sector's tipping point
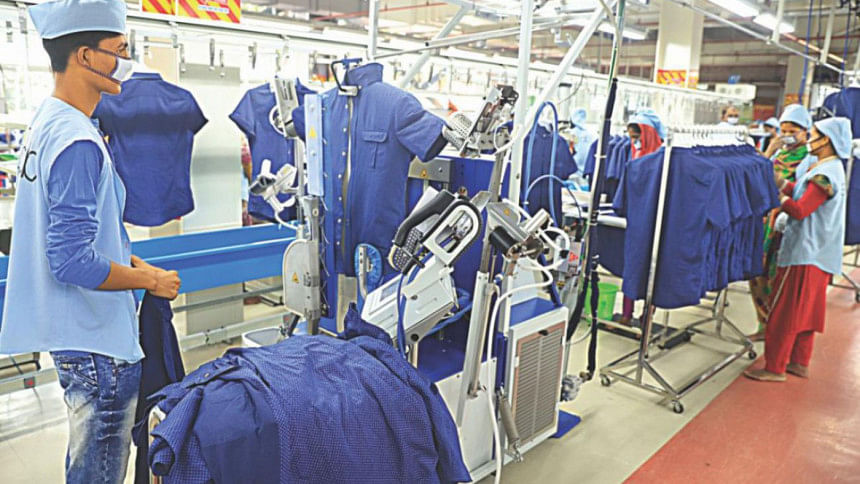
Offshoring of apparel manufacturing has been a blessing for many developing countries. The readymade garments (RMG) industry, employer of 4 million workers, mostly rural women, contributes more than 80 percent to Bangladesh's export revenue. Low-cost labour has been the primary reason for western retailers to wait for months to get a shipment from offshore destinations. Once technology becomes a cheaper alternative to the least costly manufacturing labour, will apparel manufacturing complete the journey in returning home?
As countries like Bangladesh, Vietnam or Cambodia do not have the technological edge in apparel making, why should economics of automation suggest that they should remain the cheaper alternative? With advances in robotics and automation, reshoring is bound to happen. The challenge is to detect the tipping point so that both premature exit and prolonged stay could be avoided in minimising the loss.
It's well understood that apparel making is an incredibly labour-intensive process. Starting from design, pattern-making, and cutting through sewing, there appears to be 14 major steps in turning fabrics into ready-made garments. Even in this age of automation, human intervention is quite necessary at every stage of production. But there has been continuous development of technological alternatives that has introduced automation at each step—reducing the need for labour. Automation in the form of computer-aided design and machine-assisted cutting is already in practice.
Among all the stages of apparel production, sewing is perceived to be notoriously difficult to automate.
Despite the success in cutting fabric, for instance, and sometimes sewing buttons or pockets, failure to automate the aligning of material correctly to the sewing head, feeding it through and constantly adjusting the fabric to prevent it slipping and buckling, means that there is no automated production line in which fabric goes in at the one end and finished garments, such as jeans and t-shirts, come out on the other. But recent developments indicate that this critical barrier has been overcome. A start-up in Georgia (US) has developed a highly calibrated machine vision innovation to watch and analyse fabric—succeeding in detecting distortions and robotically adjusting the fabric, while feeding to sewing head. Such automated sewing technology has successfully demonstrated that a t-shirt making plant working under the guidance of a single human handler, can produce as many shirts per hour as about 17 workers in a similar production line in Bangladesh or Cambodia. This development indicates that we are now not too far from a time when automation will make machine intensive production cheaper than labour.
The next question is, how much automation is enough to take apparel manufacturing to the tipping point of reshoring—taking back production from offshore destinations. Research suggests that within an off-shored manufacturing operation, an increase by one robot per 1,000 workers is associated with a 3.5 percent increase of reshoring activity. On average, a single robot usually takes the job of 6 workers. In apparel manufacturing, the delegation of roles from human to machine takes place in different forms, starting from the deployment of robots for handling packages to micro level automation in feeding fabrics to sewing head. Such diverse forms of automation often make it difficult to develop a prediction model based on robot density.
Another measure could be measuring the effect of automation on the reduction of labour requirement in foreseeing the tipping point of reshoring. Economics of the total cost of production suggests that reaching a completely human free state is not required to justify the relocation of plants from offshore locations. The example of Adidas relocating its manufacturing to high-wage countries such as US and Germany, employing 160 people as opposed to 1,000 workers in a comparable factory in Asian countries like Indonesia or Vietnam, indicates that once automation replaces workers up to a certain level, the tipping point of reshoring can be reached. Other factors such as cluster effects should also be taken into consideration in fine tuning such prediction model influencing business decisions.
Historically, as countries develop and wages rise, the apparel-making trade moves on to the next cheapest location: from western countries to developing ones like China and Bangladesh. Due to technological progression, instead of moving to the next cheapest labour destination, apparel manufacturing is about to return next door to the major retailers. As progress is being made in incorporating an increasing level of robotics and automation, labour cost advantage in apparel manufacturing in the age of the Fourth Industrial Revolution has been continuously eroding. There is no doubt that smart machines will keep progressing in reducing low skilled labour requirement, consequentially reshoring apparel manufacturing. The challenge for existing offshore destinations is to predict such trend and remain in sync—as both premature exit and overstay are harmful.
M Rokonuzzaman, Ph.D., is Professor, Department of Electrical and Computer Engineering, North South University, Dhaka. Email: [email protected]
The published version of this article read that the RMG industry employs 40 million workers. It has been corrected to 4 million. We regret the error.
Comments